When designing a new home build or renovation, one important decision is selecting the optimal floor framing system. The two main options are I-joists and floor trusses, each with their own strengths and weaknesses. In this post, we’ll compare the energy efficiency, cost, load capacity, installation, and environmental impact to help you decide whether to span farther with floor trusses or save money with I-joists.
An Introduction to Floor Trusses and I-Joists
Before diving into the details, let’s briefly explain what floor trusses and I-joists are:
- Floor Trusses – Constructed from wooden chords and webs arranged in interconnected triangles, floor trusses are highly customizable for each building project.
- I-Joists – With an I-shaped cross-section consisting of top and bottom chords and vertical webs, I-joists come in standard lengths and are commonly made from laminated veneer lumber.
While both can adequately support floors, there are some key differences when it comes to cost, strength, installation, and sustainability.
Energy Efficiency Comparison
An often overlooked consideration is the energy efficiency that floor framing allows. Here, the advantage likely goes to floor trusses:
- The triangular shape and open web design create space for thicker insulation.
- Can reduce air leakage and thermal bridging.
- Limits settling issues that lead to cracks and drafts developing.
With floor trusses reducing pressure on the exterior walls and ceilings, there are also fewer cracks for heat or cool air to escape. Homeowners can experience lower monthly energy bills from the improved efficiency.
Cost Comparison
For many builders and homeowners, cost is the pivotal factor driving decision-making:
I-Joists | Floor Trusses |
– Less expensive due to standardized materials and sizing | – Complex, customized design is more expensive |
– Limited customization options | – Adjustable for specialized applications to save money elsewhere |
– Easier installation can reduce labor costs | – Stronger materials support longer clear spans to reduce need for load bearing walls |
Ultimately, opting for I-joists typically comes at a lower initial price point but floor trusses offer more complexity to reduce expenses during framing and finishing work.
Bearing Heavy Loads with Floor Trusses
The next key consideration looks at the load bearing capabilities of each system. In particular:
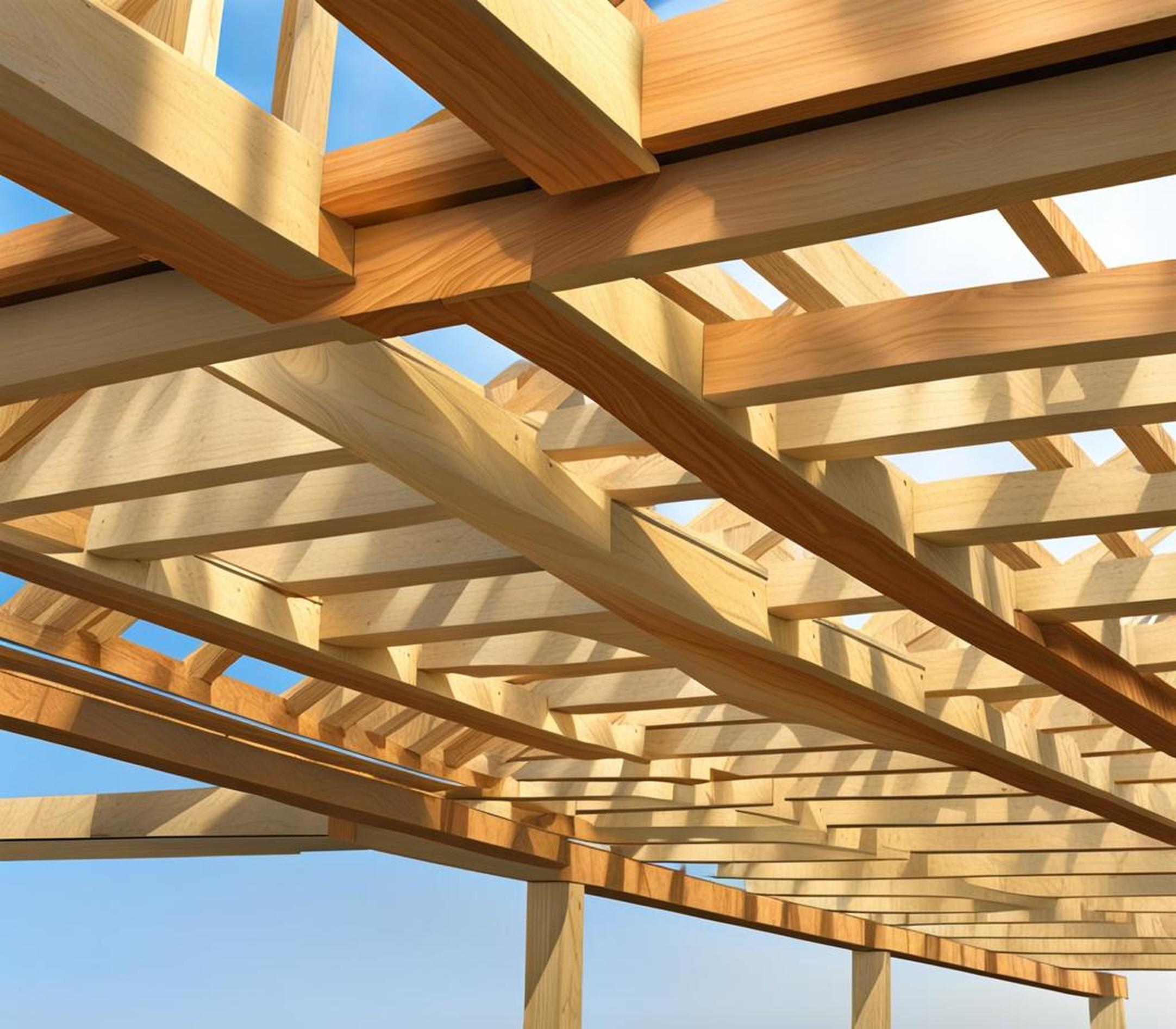
- The larger, multi-ply solid wood and metal connector plates used in truss construction result in higher strength and rigidity.
- This allows trusses to span greater lengths without intermediate support beams.
- Makes trusses well suited for upper levels of multi-story homes.
Comparatively, I-joists depend more on lightness rather than robustness. While cost-effective for typical residential loads, they become less optimal for oversized custom homes requiring larger clear spans.
The Simplicity of Installing I-Joists
Shifting gears to installation challenges highlights further distinctions:
I-Joists | Floor Trusses |
– Standard sizing quickens installation time | – Require engineered drawings and shop fabrication |
– Lightweight compared to solid lumber | – Complex structures and customization complicate installation |
With standardized dimensions, stackability for transport, lighter individual weight, and no custom components, contractors often find I-joists simpler to handle and install compared to intricate and heavy floor trusses.
Environmental Impact Factors
A final angle addresses the environmental impact of floor trusses versus I-joists:
- Optimal spacing in trusses means less raw lumber is wasted.
- LVL lumber in I-joists uses less old growth timber and glues.
- Off-gassing of VOCs may be a concern in certain I-joist products.
- Recyclability and sustainability certifications like FSC or SFI should be examined.
When sourcing materials responsibly, both floor systems can achieve eco-friendly objectives for green home builders. Lifecycle assessments help qualify any differences in pollution, carbon footprint, or waste.
Knowing the Best Applications for Each
With the major factors weighed, we can summarize when floor trusses or I-joists represent smarter selections:
Ideal Uses for Floor Trusses
- Long, open floor spans
- Upper levels of multi-story buildings
- Heavier anticipated loads
- Homes desiring energy efficiency
- Custom designs with complex architectural details
Ideal Uses for I-Joists
- Cost-driven projects with firm budgets
- Homeowner installations and DIY work
- Single story or smaller footprint designs
- Standardized construction needs
In many cases, a combination approach utilizing each system where it functions best proves optimal. This emphasizes having thorough conversations with your architect and builder to tailor floor plans to your spatial, performance, and financial needs.
Floor trusses shine for maximizing clearance beneath living areas and resisting heavy structural loads across upper levels. Yet for single floor or smaller homes, I-joists deliver reliable strength with quicker installation and fewer upfront expenses. Assessing the priorities for energy efficiency, overall cost savings, load capacities, construction complexity, and sustainability makes choosing between floor trusses or I-joists clearer.
Keep in mind that the most cost-effective decision typically aligns with smooth installations reducing job site overhead for contractors. This allows focused resources toward ideal framing materials rather than absorbing higher labor or delay expenses. With some careful planning and foresight during the design process, your dream home can take advantage of both trustworthy floor trusses and value-oriented I-joists across different areas.