Transporting large quantities of bottled water requires loading the bottles or jugs efficiently onto pallets. But before those pallets hit the road, rail, sea, or air, it’s essential to determine the total weight of the loaded pallet. Knowing the accurate pallet weight is crucial for calculating shipping costs, complying with weight limits, loading trucks safely, and preventing accidents during transit.
For a standard 40″ x 48″ wooden pallet loaded with water, the total weight typically falls between 1,000 and 1,200 pounds. However, the exact weight depends on several important factors. The type of bottles or jugs used, how tightly they are packed, and any wrapping or packaging materials can all impact the final poundage.
In this article, we’ll look at the key elements that affect pallet weight. We’ll discuss techniques for properly weighing loaded pallets prior to shipping. And we’ll examine why proper handling procedures based on weight are vital for secure transportation. Let’s dive in to learn how to measure pallet weight like a pro!
Typical Weight Range for Pallets of Water
As a general rule, a standard 40″ by 48″ GMA pallet loaded with water bottles or jugs will weigh 1,000 to 1,200 pounds. This average weight range depends on the most common factors:
- Bottle/jug size – Smaller bottles weigh less per pallet than larger jugs
- Pallet load configuration – Stack alignment and tightness affect weight capacity
- Wrapping/packaging – Materials like stretch wrap add minor weight
Shippers may load pallets with cases of twelve 16.9 oz water bottles, or larger 1 gallon jugs for office water coolers. Naturally, the heavier gallons lead to greater overall pallet weight. But even for the same bottle size, variables like bottle material (plastic vs. glass) and packing density cause weight fluctuations.
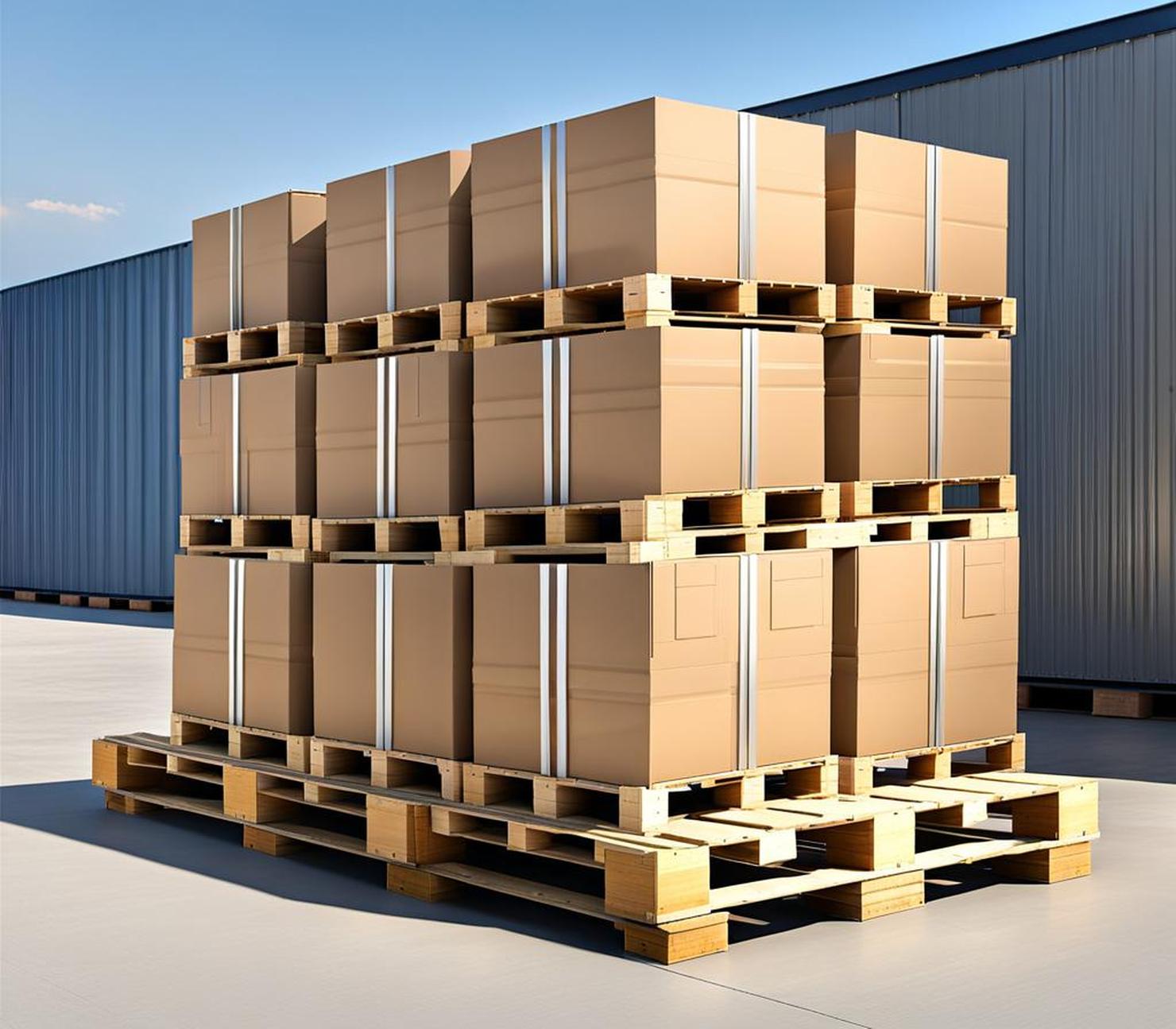
While 1,000 to 1,200 pounds is typical, customized pallets allow even heavier loads. For example, a pallet measuring 48″ x 56″ could potentially accommodate 50% more water weight. The main point is that standard pallet sizes and bottle configurations provide a reasonable weight estimate.
Elements That Impact Pallet Weight
To hone in on your exact loaded pallet weight, it’s important to look at the specific factors involved. Subtle variations in these elements can add up to significant differences in total poundage.
Bottle/Jug Size
The most obvious factor determining pallet weight is the size of bottles or jugs used. Some key size comparisons:
- 12 oz bottles = 24 lbs per case
- 16.9 oz bottles = 28 lbs per case
- 1 gallon jugs = 38 lbs per case
- 2.5 gallon jugs = 63 lbs per case
For the same pallet dimensions, larger bottle sizes translate to higher weight. Gallons outweigh standard 12 or 16 oz bottles by over 50%. So a pallet packed tightly with gallons can weigh 150-200 lbs more than lighter bottles. Choosing the right bottle size for your needs is the first step.
Pallet Size
The length, width, and height of your pallet also determines maximum load capacity. Common sizes include:
- 48″ x 40″ GMA pallets – Typical for high-volume bottled water
- 48″ x 45″ pallets – More weight capacity
- Custom sizes like 48″ x 56″ – For heavier loads
Oversized or custom pallets allow you to stack more layers of water bottles. This directly translates into increased overall weight. Just ensure your pallet choice matches your shipment needs and equipment capabilities.
Load Configuration
How tightly and efficiently the pallet is packed affects the density and stability of the load. A pallet stacked with proper alignment and minimal gaps can accommodate more weight before hitting capacity.
Poorly aligned stacks are more prone to leaning and tipping. Avoid uneven or unstable loads by packing bottles squarely and tightly. Utilize the entire surface area and maximize vertical space for dense, secure pallets.
Wrapping/Packaging
Using pallet wrapping materials helps secure the load for shipment. Stretch wrap, shrink wrap, and plastic strapping add stability but also slightly increase pallet weight. Consider the wrapping method based on load needs:
- Stretch wrap – Up to 6 ounces per pallet
- Shrink wrap – Up to 16 ounces
- Plastic strapping – Up to 8 ounces
Factors like pallet edge protectors, box reinforcement, and water-resistant wrapping for outdoor loads also contribute marginally to overall weight.
Why Accurate Weight Matters
Determining true pallet weight is so important because it directly impacts key transportation requirements and costs:
Calculate Shipping Costs
Carriers base transportation rates on total weight. Underestimating pallet weight leads to billing shortfalls and losses. Overestimating causes overpayment. Weigh each pallet after loading to get exact weights for precise freight costing.
Ensure Compliance with Weight Limits
Truck, air, rail, and sea freight methods all have weight restrictions. Exceeding these limits results in rejected shipments and penalties. Know your weight to avoid regulatory fines.
Load Trucks Safely
Loading overweight pallets can overload trucks and trailers. Improper weight distribution leads to dangerous instability. Accurately weighing pallets enables ideal truck loading patterns.
Prevent Accidents from Overweight Pallets
Excess pallet weight limits handling safety. Forklifts and pallet jacks can fail under extremely heavy loads. Overweight pallets also break truck axles and cause rollovers. Weigh pallets to prevent cost and liability from accidents.
Weighing Loaded Pallets
To get accurate pre-shipment pallet weights, use one of these recommended methods:
Warehouse Floor Scale
Floor scales like a pallet scale placed in the shipping area offer precise loaded pallet weights. Roll the stacked and wrapped pallet onto the platform for an exact total.
Pallet Truck Scale
Specialized pallet jack scales allow weighing pallets right in the warehouse aisle. Hydraulic and digital models provide precise weight data from the forklift.
For both options, be sure to tare off the scale first without the pallet. Weigh the loaded pallet after all wrapping and materials have been added for true net weight.
Account for Pallet and Wrapping
Remember to add the tare weights of the pallet, stretch wrap, and other packaging into total weight calculations. This ensures accurate freight costs and compliance.
Safe Handling Based on Weight
To promote safety when moving heavy pallets, follow these weight-related precautions:
Use Properly Rated Equipment
Know your pallet jack and forklift capacity limits based on tested load centers. Select models rated for your verified pallet weights.
Review Weight Before Transporting
Confirm total pallet weight before attempting to lift or transfer with any equipment. Avoid assumptions to prevent overloading.
Load Secured Pallets on Trucks
Use load bars, straps, and friction mats to properly secure heavy pallets on trailers based on weight. Prevent load shifts that cause handling issues.
When shipping truckloads of bottled water, accurately determining pallet weight is crucial. While 1,000 to 1,200 pounds is typical for standard pallets, bottle size, pallet dimensions, load configuration, and wrapping impact the total. Weigh fully loaded pallets to calculate freight costs, meet weight limits, load trucks safely, and avoid transit accidents.
Knowing precise pallet weight upfront takes the guesswork out of water shipments. Weighing pallets properly and taking appropriate safety precautions gives you confidence at every step in the supply chain. When armed with accurate pallet weights, you can ship every order smoothly from warehouse to customer.