Upgrading your home’s electrical service to 100 amps gives you the capacity to run multiple high-wattage appliances and devices simultaneously. However, in order to handle the increased electrical load safely, you need adequate wiring sized for a 100 amp circuit. Aluminum wire is an affordable and practical option for large 100 amp installations. But with its particular properties and code requirements, getting the right aluminum wire size can be tricky.
We’ll look at how aluminum compares to copper, go over wire gauge sizes and ampacity ratings, explore National Electrical Code (NEC) rules, and make recommendations for appropriate wire gauges. We’ll also discuss important best practices for installing and working with aluminum wire to avoid safety issues. Finding the right balance of cost and performance requires understanding aluminum wire’s unique characteristics.
Wire Basics: Aluminum vs. Copper
The most common residential wiring types are copper and aluminum. Though copper has been the traditional choice, aluminum has gained popularity due to its lower cost, lighter weight, and higher conductivity. However, aluminum also comes with some downsides.
Aluminum has about 61% the conductivity of copper per unit cross-sectional area. What does this mean? For the same gauge wire, copper can carry more current than aluminum before overheating. To equal copper’s ampacity, aluminum needs a greater cross-sectional area–in other words, a thicker wire gauge.
For small branch circuit wiring like 15 amp and 20 amp circuits, copper is generally preferred. But aluminum is cost-effective for large 100 amp feeders and service entrance cables. The larger gauge aluminum wire required for 100 amps offsets its lower conductivity.
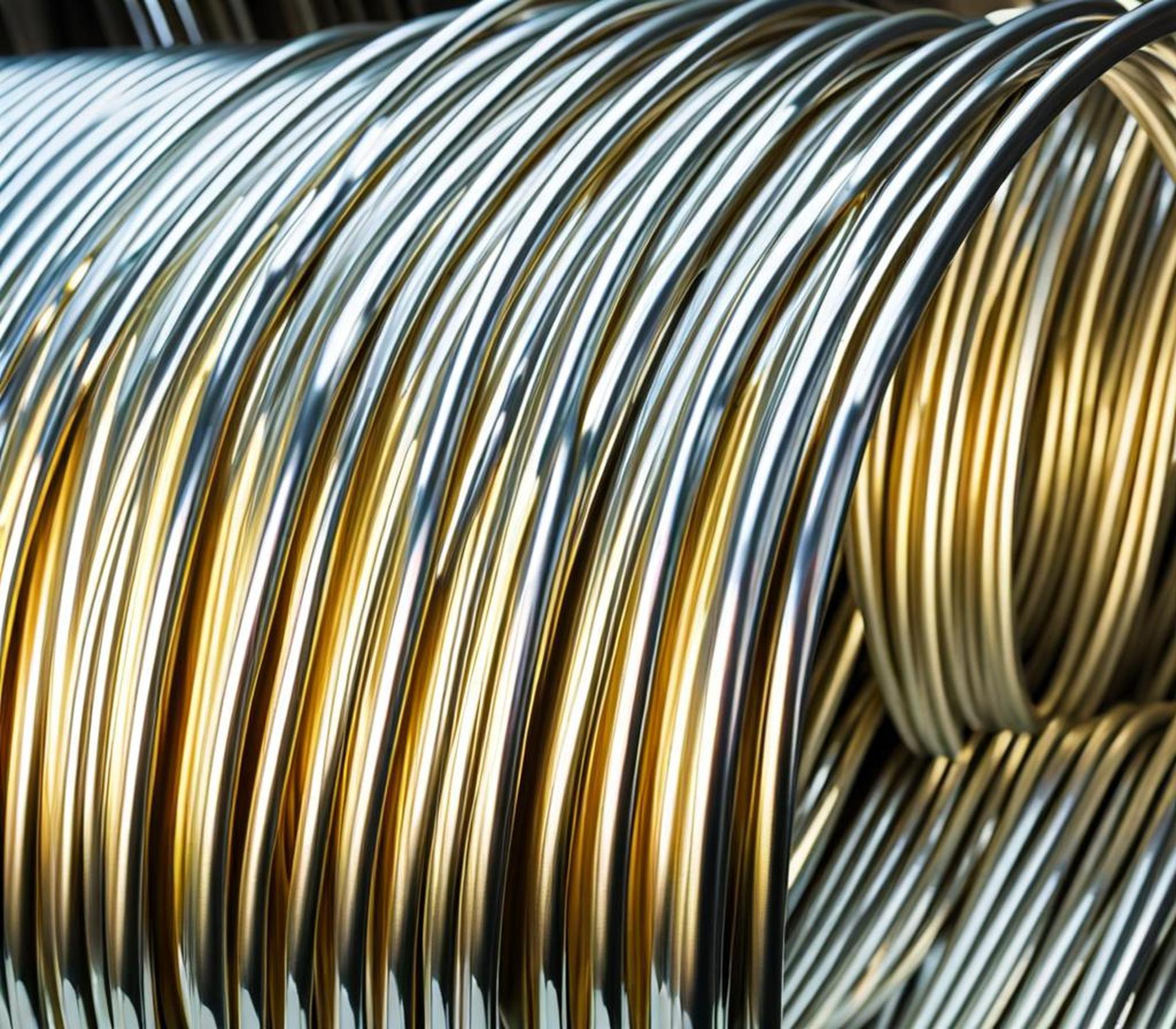
Besides conductivity, a few other key differences exist between these two conductor metals:
- Aluminum is lighter in weight than copper, making it easier to work with and install.
- Aluminum wiring is cheaper upfront. However, the larger sizes needed can offset some savings.
- Aluminum has a higher coefficient of expansion than copper. This requires special installation methods to prevent loose connections.
- Aluminum is more vulnerable to oxidation and corrosion, necessitating antioxidant paste and rated connections.
Now that we’ve compared copper and aluminum, let’s look at wire sizes…
Understanding Wire Gauge Size and Ampacity
Wire gauge refers to the diameter of the conductor metal inside the insulation. In North America, gauge size is denoted using the American Wire Gauge (AWG) system. Wires have a gauge number that gets smaller as the wire gets thicker. For example, a 10 AWG wire is thicker than a 12 AWG wire.
With both copper and aluminum, a thicker wire gauge allows safely carrying more current and power. This maximum current-carrying capacity or “ampacity” varies not just by gauge, but also by:
- Material (copper vs. aluminum)
- Insulation type
- Ambient temperature
- Single vs. bundled conductors
Ampacity charts in the NEC provide the rated capacities for different wire types under assumed conditions. These are based on limiting conductor temperature rise to avoid insulation damage. While copper wiring uses the standard ampacity table, aluminum has lower ampacity and requires consulting an adjusted table.
Ampacity Adjustments for Aluminum Wire
Due to its higher resistance and heat generation compared to copper, aluminum wire requires special ampacity de-ratings to maintain safe operating conditions. The 2015 NEC includes an ampacity correction factor of 0.89 for aluminum conductors.
What does this mean? For any standard ampacity, multiply by 0.89 to find the equivalent ampacity for aluminum wire. For example, 1 AWG copper wire has a 130 amp ampacity according to Table 310.15(B)(16) in the NEC. Applying the 0.89 factor gives 1 AWG aluminum an ampacity of only 115 amps.
Besides this blanket de-rating factor, additional adjustments may apply:
- Ambient temperature correction factors
- Reduced ampacity for more than 3 current-carrying conductors bundled together
We have to consider these derating factors when selecting aluminum wire sizes for 100 amp service.
Code Requirements for 100 Amp Aluminum Wiring
To safely accommodate 100 amps, aluminum wiring must meet certain sizing requirements specified by NEC articles 310.15 and 240.4(D). Let’s look at some key provisions:
Minimum Aluminum Wire Size
NEC Table 310.15(B)(16) sets minimum sizes for aluminum conductors. For a 100 amp circuit, the minimum aluminum wire size is:
- #1 AWG for a single conductor
- #3 AWG for multiple conductors in a raceway or cable
Smaller gauges may be prone to overheating at 100 amps even after ampacity de-ratings. The minimum sizes ensure safe, reliable high-capacity service when properly installed.
Rating for Continuous Loads
Per NEC 240.4(D), we must rate wiring for continuous loads at 125% of the ampacity. This covers electrical services with expected continuous current for 3+ hours. For 100 amp non-continuous loads, #1 AWG aluminum is fine. But for a 100 amp continuous service, minimum size increases to #1/0 AWG based on 125% sizing.
Bigger Wire for Aluminum
Even when meeting the minimum sizes above, aluminum wire MUST be one size larger than copper for an equivalent ampacity after de-ratings. So where 1 AWG copper would suffice for 100 amps, 1 AWG aluminum requires upsizing to #0 AWG to compensate for the reduced capacity.
The code aims to offset aluminum’s lower conductivity by mandating thicker wire. This prevents safety issues from insufficient ampacity.
Recommended Aluminum Gauges for a 100 Amp Service
Based on the NEC code requirements and typical 100 amp service specs, two aluminum wire sizes emerge as suitable options:
1 AWG Aluminum Wire
With its higher ampacity, #1 AWG aluminum wire is a great choice for 100 amp circuits in many circumstances:
- Meets NEC minimum size for a single conductor
- Works for up to 115 amps continuous capacity after derating
- Recommended for long wire runs due to lower voltage drop
- Allows for future expansion to 125+ amp service
The downside is 1 AWG aluminum is more expensive and stiffer than smaller gauges. Use is typically limited to service entrance cables and interior main feeders.
3 AWG Aluminum Wire
For most 100 amp residential services, #3 AWG aluminum wire offers a good balance of cost and performance:
- Meets NEC minimum size for multiple conductor cables
- 100 amp rating after standard 0.89 derating factor
- More flexible compared to larger 1 AWG
- Cost-effective for runs up to 100 feet in length
Limitations of 3 AWG aluminum include greater voltage drop over longer distances and inability to handle continuous loads over 100 amps.
Choosing between 1 AWG vs. 3 AWG depends on the specific electrical loads and installation requirements…
Comparing 1 AWG vs. 3 AWG Aluminum
Weigh the following factors when deciding size for your 100 amp service:
- Continuous loads – 1 AWG for over 100 amps continuous; 3 AWG for 100 amps or less
- Conductor length – 1 AWG better minimizes voltage drop in long runs
- Ampacity margins – 1 AWG allows more room for future expansion
- Conduit fill – 1 AWG uses more space in crowded conduits
- Budget – 3 AWG offers significant cost savings over 1 AWG
An electrician can help determine the ideal aluminum wire gauge for your specific electrical service needs while following code.
Installation Considerations for Aluminum Wiring
Once you’ve selected the appropriate aluminum wire size, proper installation is crucial. Let’s look at some key guidelines.
Making Safe and Reliable Connections
Aluminum wire’s tendency to oxidize can lead to faulty connections if not addressed. Use only connectors approved for aluminum such as copper double compression sleeves. Coat all connections with antioxidant paste to prevent oxidization.
Tighten connections to the manufacturer’s specifications using calibrated torque wrenches to avoid looseness. Loose connections cause dangerous overheating.
Allowing for Thermal Expansion
Aluminum expands nearly twice as much as copper when heated. Leave room for wire expansion by using oversized conduits and avoiding tightly binding bundles.
Stranded aluminum wire handles expansion better than solid core wire. See NEC 310.15(B)(3)(a) for installation guidelines.
Maintaining Proper Bending Radius
Sharply bending aluminum wire leads to work hardening and breakage over time. Maintain a minimum bending radius to avoid damage:
- 4x wire diameter for 1-1/0 AWG and smaller
- 5x wire diameter for 2-4 AWG
Carefully dress wires around corners and junction boxes to prevent kinks.
Following Code Requirements
Adhere to NEC rules for securing wires, limiting conduit fill percentage, providing protection from physical damage, proper grounding and bonding, and other safety-related provisions.
Working With Electrical Professionals
While DIYers can safely install their own home wiring in many cases, large aluminum circuits have greater complexities. Consult a professional electrician when uncertain about:
- Recommended aluminum wire size for your electrical load
- Ampacity adjustments based on ambient temperature
- Derating for number of current-carrying conductors
- Inspection for improper connections or installation issues
They can also demonstrate proper techniques for working with aluminum wire to avoid common mistakes.
Upgrading your electrical service to 100 amps gives you the capacity to run multiple large appliances and devices. But it also requires properly sized aluminum wiring to handle the higher electrical load safely.
Choosing aluminum wire in the appropriate gauge as outlined by the NEC ensures your 100 amp circuit has sufficient capacity. Common options are 1 AWG for larger continuous loads and long runs, or 3 AWG for shorter general home circuits.
Pay close attention to special installation needs for aluminum such as rated connectors, antioxidant paste, expansion gaps, and bending radius limits. And don’t hesitate to call in a professional electrician whenever you have questions or concerns about working with aluminum wire.
Selecting the right size aluminum wire for your home’s 100 amp electrical service will allow you to upgrade capacity without safety issues. Just be sure to follow code requirements and manufacturer specifications throughout the installation process.