Installing screws into metal studs presents unique challenges not found with wood studs. The dense, rigid surface of metal defies standard screws, resulting in spinning, stripped threads, and failed connections. Simply using the wrong fastener can spell disaster in a metal framing project.
Selecting the optimal screw is crucial for proper installation and durable connections with metal studs. But with so many options on the market, how do you determine the best screw for your specific needs?
Sharp Tip is Essential for Penetrating Metal
The first requirement of any screw going into metal is a sharp tip. The high hardness and density of metal studs demand a pointed end to bite into the surface. Standard flat head screws are likely to slip, walk, or skate off the metal when driving them in.
A sharp screw tip reduces resistance and effort needed to initiate driving into the rigid material. The pointed end wedges into the metal more easily and centers the screw properly for straight entry. Dull or blunt tips often fail to penetrate the tough exterior of metal studs.
Self-Piercing and Self-Drilling Screw Tips
For very thick or heavy gauge metal studs, specialized self-piercing and self-drilling screw tips can save time and effort. These unique tips combine a drill point and tapered end that can bore into the metal while simultaneously cutting internal threads.
The ability to tap threads and create a pilot hole in one step eliminates the requirement for pre-drilling holes. Self-piercing tips are quick and convenient for dense materials where pre-drilling would be tedious and time-consuming.
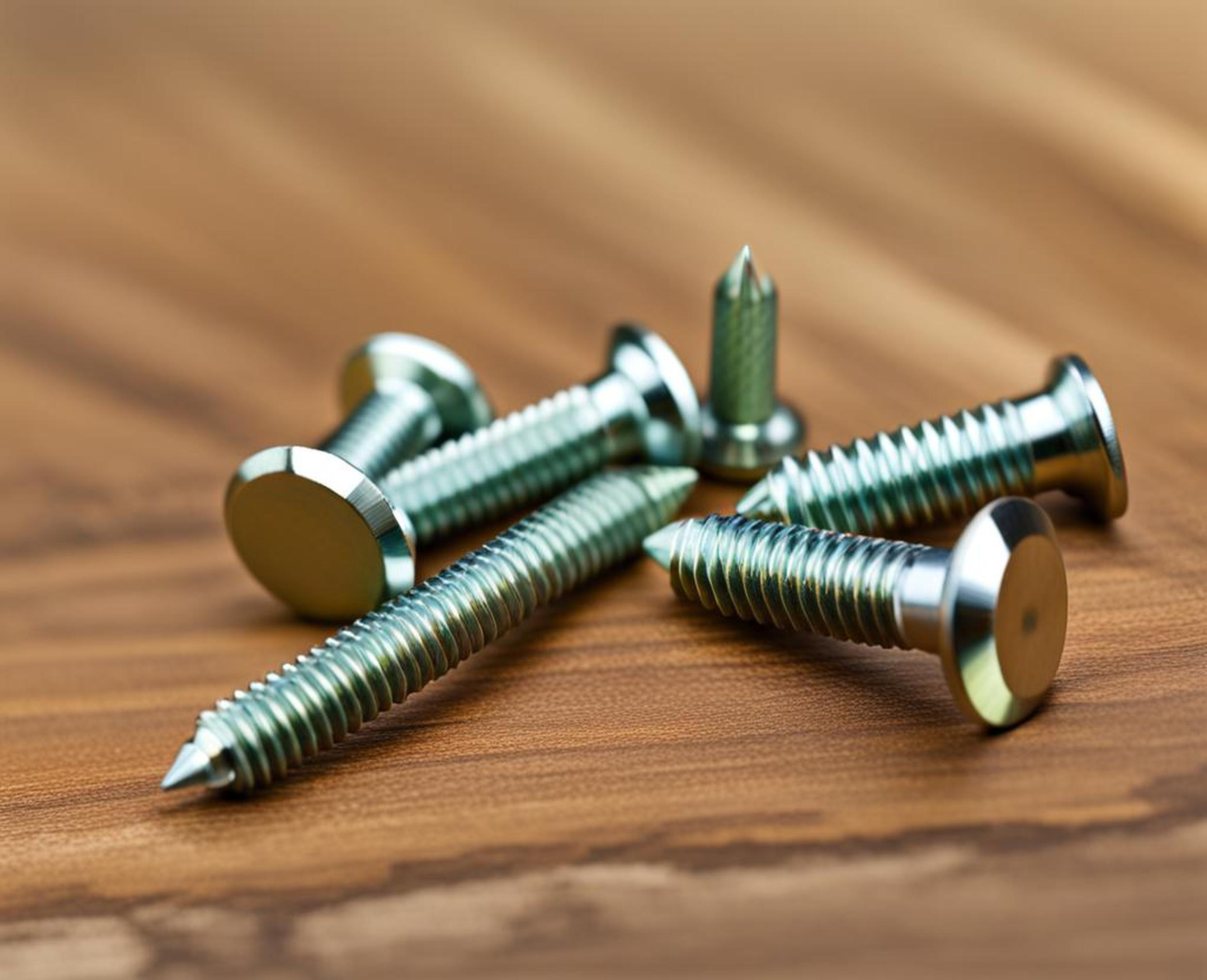
Drill-Point Tip Drives Straight Into Metal Studs
While a standard conical tip can penetrate metal, it tends to wander and veer off course when starting. This leads to misaligned screw holes and uneven connections.
A drill-pointed tip shaped like — well, a drill bit — guides the screw precisely into the metal surface. The center point secures the screw into the stud before the threads engage. This prevents screws from sliding around and ensures consistent fastening.
The drilling action of the tip maintains a straight driving angle. The screw turns effortlessly into the stud, without the binding or seizing that can occur with uneven angled entry.
Fine Threads Crucial for Holding Power
Coarse, widely spaced threads common on wood and drywall screws fail catastrophically in metal. The sparse threads concentrate force over a smaller surface area in hard metal. This leads to stripped threads and reduced grip strength.
Finer, closely-spaced threads distribute force across more area. This greatly reduces the risk of tear out when driving screws into metal studs. The improved surface contact enhances holding power once installed.
Optimal Thread Count and Pitch
Higher thread count means more threads engage the surrounding metal, improving resistance to pull-out. However, too many fine threads can overload a screw when driving it. Finding the right balance is key.
The thread pitch, or number of threads per inch, also factors in. Follow the manufacturer’s recommendations for optimal pitch and thread count for specific applications.
Necessary Material Properties
Metal studs demand screws made of the toughest, most durable materials to withstand their unforgiving hardness. Two material properties are paramount:
Strength
The material needs tremendous shear and tensile strength to penetrate metal, resist snapping on drive-in, and support load. Stainless steel, carbon steel, and alloy steel screws deliver the ideal strength.
Their exceptional hardness drives into metal without bending, deforming, or mushrooming. They withstand high torque and forces without failure.
Ductility
Some degree of flexibility and ductility prevents fatigue and cracking from metal’s rigidity. Stainless steel has greater ductility than carbon steel, allowing more flexibility and impact resistance.
The material must also hold threads securely without stripping. Ductility enables screws to flex slightly rather than shear off in unforgiving metal.
Critical Corrosion Resistance
Standard steel rapidly corrodes and rusts when exposed to moisture, creating weaknesses. Stainless steel contains chromium that forms an invisible passive layer making it inherently corrosion resistant.
Otherwise, protective coatings must shield screws from the environment. Common options include:
- Zinc coating
- Ceramic coating
- Black oxide
Compare coating methods to choose screws that best resist corrosion, chemicals, and moisture over time.
Sufficient Screw Length
Using a screw long enough for the application ensures complete penetration into both connected materials. Too short leaves a gap while too long risks poking through the other side.
Follow manufacturer guidelines for proper lengths. Allow for layering of finishes or overlapping materials. Leave at least three exposed threads protruding past the metal stud for optimal strength.
Avoid excessively long screws extending wastefully beyond the stud depth. This risks hitting utilities within wall cavities.
Wide, Thick Screw Head
Screw heads play a vital role in metal connections. Narrow, low profile heads like those on drywall screws are prone to pull-through failures.
Wide heads with deep socket contacts distribute force over more area. This greatly reduces torn out screw heads in the hard material.
Look for pan heads, washer heads, hex heads, or other large screw heads to maximize surface area. The improved contact helps prevent stripping while reinforcing the connection.
Proper Screw Spacing
Crowding too many screws close together in a metal stud leads to uneven loading. Follow manufacturer spacing guidelines for pilot holes and screw placement.
Proper spacing ensures:
- Load balances across stud
- Prevents metal fatigue or cracking
- Allows full embedment into stud
Too many crowded screws risk compromised holding strength and damaged studs. Take care to space screws correctly for optimal connections.
The right screws make all the difference when working with metal studs. Sharp, self-drilling tips, fine thread counts, super-strong steel construction, rust-resistant coatings, and wide heads distinguish screws engineered for metal.
Choosing appropriate screws prevents spinning, stripping, and breaking in metal studs. This saves immense time, money, and frustration addressing failed connections on the job site or after installation.
You can choose screws based on criteria like drill points and high shear strength.