Hydro Flask has become one of the most recognizable brands of reusable water bottles and insulated drinkware on the market today. Known for their unique TempShield vacuum insulation technology, Hydro Flask bottles can keep drinks cold for up to 24 hours or hot for up to 12 hours. But have you ever wondered exactly how these popular bottles are made?
In this in-depth article, we’ll take a close look at Hydro Flask’s full manufacturing process. We’ll explore why the company chose to produce their bottles in China, the facilities and standards used in production, and the step-by-step process required to create their double-walled, vacuum sealed designs. By the end, you’ll have an inside look at how Hydro Flask has consistently delivered high-quality and innovative drinkware for over 10 years.
Manufacturing Bottles in China
Why Hydro Flask Chose China
While Hydro Flask was founded in Oregon in 2009, the company has always manufactured their bottles in China. This is primarily due to China’s expertise and capabilities when it comes to stainless steel manufacturing. Hydro Flask uses grade 18/8 stainless steel for their bottles, which requires injection molding processes that are most efficiently done in high-volume Chinese factories.
Producing at scale in China also allows Hydro Flask to meet demand and control costs. As a young startup brand, having the production capacity to supply major retailers was critical to Hydro Flask’s growth. Sourcing materials, components, and manufacturing in China enabled the rapid expansion that put Hydro Flask bottles into millions of hands.
The Manufacturing Facility
Hydro Flask works closely with a major bottle production facility located in the Guangdong province of southern China. The massive 1.5 million square foot factory has a daily capacity of over 150,000 bottles across several production lines dedicated to Hydro Flask.
The facility has all the capabilities needed to transform raw stainless steel into finished Hydro Flask products. This includes metal fabrication stations, plastic injection molding machines, printing/labeling equipment, and proprietary sealing/insulation technology.
Adhering to Standards
Hydro Flask maintains rigorous quality control standards for all outsourced manufacturing. Their suppliers in China are regularly audited to ensure facilities meet ethical working conditions and business practices.
On the production line, each manufacturing step must adhere to Hydro Flask specifications. This covers materials used, equipment parameters, manufacturing methods, and quality assurance testing. For example, steel thickness, grade, and composition must meet requirements to maintain bottle durability.
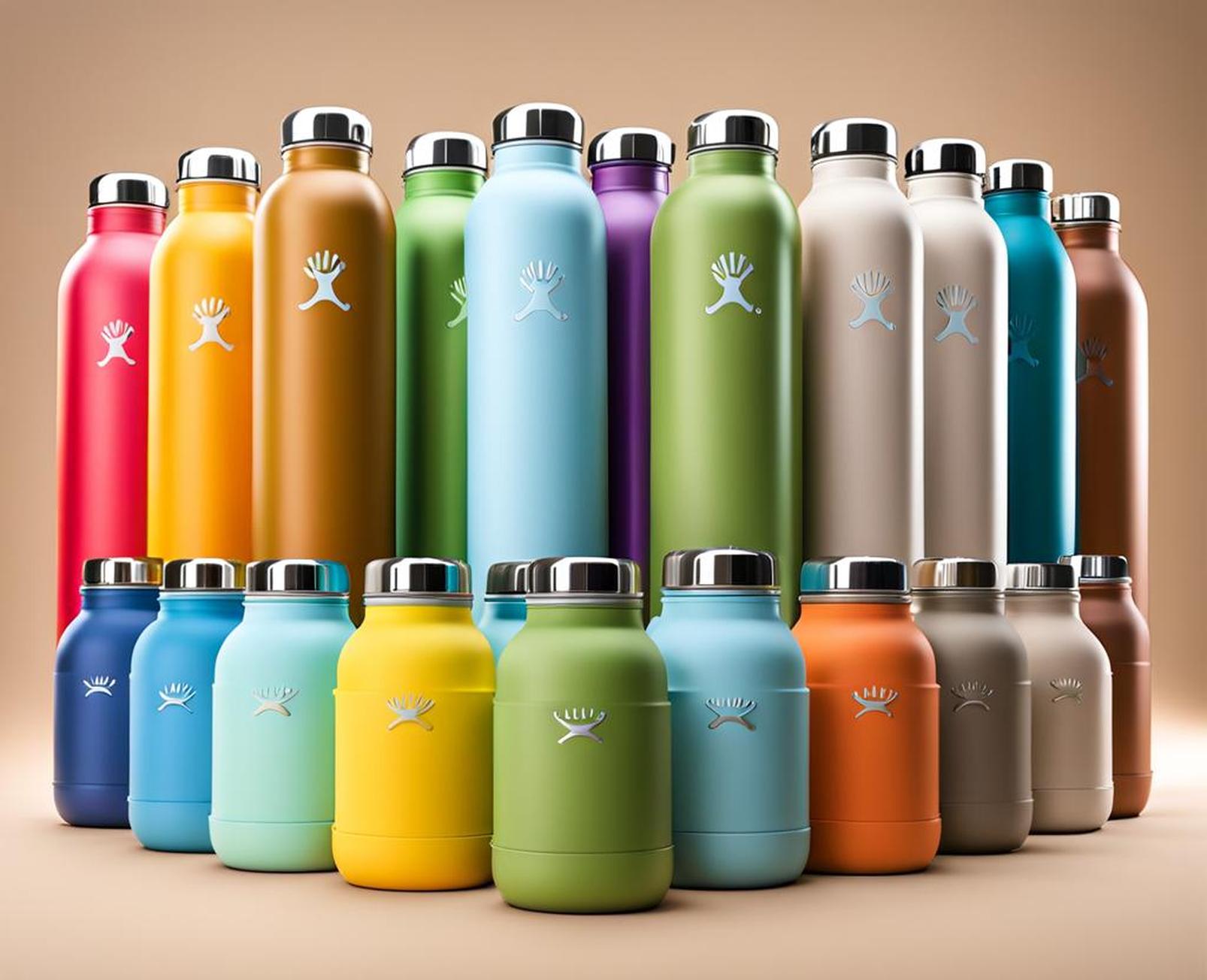
By controlling supplier standards and closely monitoring production, Hydro Flask ensures consistent quality across millions of units made in China every year.
The Production Process Step-by-Step
Proprietary TempShieldTM Insulation
The key to Hydro Flask’s performance lies in their proprietary TempShield insulation liner. TempShield is made from a lightweight, flexible foam material that contains micro-molecules designed to prevent heat transfer.
During manufacturing, the TempShield material is injected into the space between the interior and exterior bottle walls. Automated equipment then removes excess air, creating a vacuum seal critical for insulation performance. This temperature-regulating liner can be seen when inspecting the open interior of a Hydro Flask bottle.
Stainless Steel Parts
Hydro Flask uses grade 18/8 stainless steel for both the interior and exterior bottle components. The raw stainless steel is first formed into the inner and outer liners using an injection molding process. This involves heating the steel to high temperatures until it reaches a malleable state where it can be molded into shape.
Once cooled and set, the molded steel parts are polished and finished. This removes any imperfections and ensures a smooth interior with no risks of bacteria buildup. The iconic powder coated exterior colors are also applied at this stage.
Bottle Assembly
The stainless steel inner liner and outer shell are combined together by automated assemblers. The TempShield insulation liner is inserted in between the walls before sealing. The bottle cap, flexible boot, and other accessories are added to finish off the product.
At multiple stages of assembly, the bottles undergo leak and insulation tests. Samples are filled with cold and hot water to verify the vacuum seal and heat retention meet requirements. Only once passing all assessments are bottles approved to proceed.
Quality Control and Assurance
Throughout the production line and assembly process, Hydro Flask bottles are subject to rigorous quality control procedures. This includes multi-point inspections and testing at different manufacturing stages.
All bottles are visually examined for any defects and must pass pressure tests that simulate normal usage. Drop tests are conducted by letting filled bottles free-fall to check for leaks or dents. The TempShield insulation capacity is validated through temperature retention tests.
Any bottles that fail to meet standards are rejected and sent back for rework or scrap. Only bottles that pass every quality check point move on for final packaging.
Packaging and Shipping
After assembly and inspection, the finished bottles enter automated packaging stations. Here they are shrink-wrapped and loaded into corrugated boxes labeled for shipment overseas.
Loaded containers are transported from the manufacturing facility to nearby ports. The bottles are then loaded onto cargo ships bound for the United States, beginning their long transpacific journey to warehouses and stores across North America.
The Benefits of Hydro Flask’s Manufacturing Process
By combining high-volume Chinese factories with stringent oversight and standards, Hydro Flask delivers exceptional quality at scale. Instead of compromising cost for quality, Hydro Flask controls manufacturing in China to offer affordable prices to consumers while meeting exacting performance requirements.
Producing the technical TempShield insulation seal in an optimized, automated environment also improves consistency. This results in reliable temperature retention customers can count on from their Hydro Flask bottles.
And despite the long transoceanic journey, making bottles close to stainless steel suppliers in Asia minimizes shipping miles for raw materials. This reduces the overall carbon footprint compared to manufacturing in North America.
Hydro Flask’s end-to-end manufacturing techniques enable their stylish, insulated bottles to be made efficiently at large volumes without sacrificing quality or sustainability. By managing outsourced production in China while adhering to strict specifications and oversight, Hydro Flask delivers high-performance drinkware to millions globally.
So next time you reach for your Hydro Flask, you can appreciate the complex manufacturing process that goes into creating these innovative insulating bottles. It combines stainless steel molding, vacuum seal technology, and rigorous quality control to bring you a durable bottle built to last.
In recent years, there have been some reports suggesting that Hydro Flask may be considering moving some or all of its manufacturing operations out of China. In 2019, the company announced plans to build a new factory in Oregon, USA, which is expected to produce a significant portion of its products by 2022. This move is likely motivated by a desire to reduce reliance on Chinese factories, which have been subject to increased tariffs and trade tensions between the US and China.
However, it’s important to note that even if Hydro Flask does shift some production to the US, it’s unlikely that all manufacturing will be done domestically. Vacuum insulated stainless steel bottles require a complex manufacturing process, and many of the necessary materials and components are still primarily sourced from China.
Despite this, some companies have successfully managed to bring some or all of their manufacturing back to the US. For example, Klean Kanteen, another popular brand of reusable water bottles, moved its production facilities from China to factories in California and Washington. While challenging, domestic manufacturing may allow greater control over quality and reduce risks from global supply chain disruptions.
It will be interesting to see if Hydro Flask decides to fully relocate manufacturing to America. But for now, their alliance with major Chinese factories seems to provide the production capacity and technical expertise needed to make millions of high-performance insulated bottles every year.