Increasing production and efficiency is a constant pursuit in timber harvesting operations. Excavator attachments like the Lumberjack optimize workflows by integrating both felling and processing capabilities into one powerful machine.
Excavators are already utilitarian workhorses on logging sites. With an attachment like the Lumberjack tree harvester and processor, their capabilities expand even further. This precision-engineered tool can fell trees, delimb logs, and even sort them by length or diameter. It eliminates extra equipment and steps, boosting an operation’s productivity.
How The Lumberjack Attachment Works
Mounting System
The Lumberjack is purpose-built for excavators ranging from 5 to 30 tons. A universal mounting bracket allows it to be equipped or removed easily so the excavator can pivot to other tasks. Inside the cab, the operator governs the powered Hardox blade and grapple with a straightforward control panel.
Cutting System
At the heart of the attachment is the heavy-duty, hydraulically-powered felling blade made of hardened steel. It generates enough force to cut down trees of virtually any species up to 45cm thick with just a single swipe. With a full 360 degrees of visibility from the cab, operators can assess each tree and cut with precision.
Sorting/Processing Capability
The processor’s grapple can grasp multiple logs up to 130cm in diameter. This allows the machine to feed itself, sorting by length, diameter, or even species. By felling and sorting in a single step, it gets rid of a redundant stage in the harvesting process for major gains in efficiency.
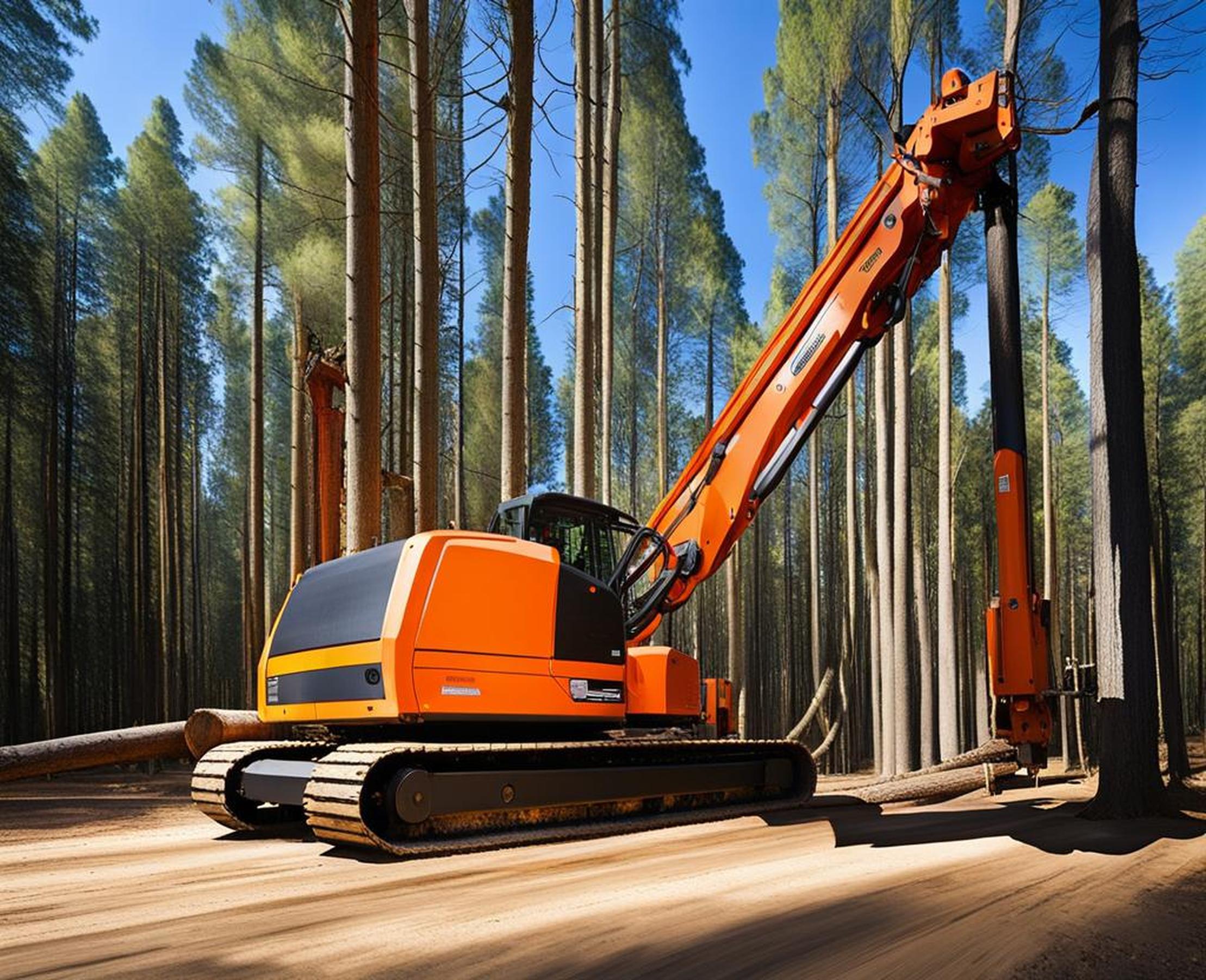
Key Features and Benefits
Precision
The Lumberjack was engineered specifically for accuracy. A large consideration was reducing unintended damage to surrounding trees. Its compact size allows it to access tight spots where harvesters can’t reach. The combination of power and maneuverability gives operators surgical control over each cut.
Efficiency
By tackling felling and post-felling sorting/processing in one seamless workflow, the Lumberjack prevents downtime from switching machinery. The grapple that does the sorting can grip multiple logs in one go for feeding efficiency. It’s the ultimate consolidation tool to help crews work smarter.
Agility and Reach
The Lumberjack leverages the excavator’s innate agility, both in traversing rough terrain and reaching tall lengths with precision. It can navigate inclines up to 40 degrees while its extension capability spots danger trees along rights-of-way. Compactness makes it ideal for thinning plots or acreages with acreages with strict removal criteria.
Durability
This attachment is built burly specifically for the grueling conditions of timber operations. The felling blade retains its hardened edge even under intense use thanks to the high-wear resistance of Hardox steel. Top-grade components like the hydraulics and grapple clamp deliver strength as well as longevity.
Types of Jobs Ideal For The Lumberjack
Thinning/Selective Cutting
In forests requiring thinning for improved growth and vigor, the Lumberjack lets operators select extraction paths to minimize disturbances. Eliminating the tree falling step first is cleaner and safer for remaining trees.
Urban Tree Removal
From residential acreages to municipal parks, the Lumberjack can remove hazard trees and invasive species without collateral damage. Variable blade positioning and a compact footprint carefully navigate property improvements and landscaping.
Right-of-Way Clearing
Rights-of-way around critical infrastructure require periodic clearing and hazard tree assessment. Here the Lumberjack excels with its quick mounting bracket to pivot the excavator between tasks like brushing and grading.
With a tool like the Lumberjack tree harvester and processor attachment, forward-looking operators gain more control over improving their workflow. Consolidating felling and sorting/processing prevents downtime from switching machinery. Ultimately, boosting productivity per machine means pulling more value from equipment investments.
From manual labor reduction to precision cutting, the Lumberjack promises operators smarter solutions for taking on more diverse jobs. Innovations like this will pave the way for modern, efficient approaches to timber harvesting operations.
Advancements in autonomous technology
While the Lumberjack and other forestry equipment mentioned are currently operated by humans, autonomous technologies are advancing rapidly. Companies are developing forestry equipment with GPS guidance, laser scanning, sensors, and artificial intelligence to enable them to navigate terrain and select trees for harvest autonomously. These autonomous forestry machines have the potential to improve efficiency, safety, precision, and minimize environmental impacts. Adoption is still in early stages but could transform future timber harvesting operations.
Use of renewable energy sources
Most logging equipment still relies heavily on diesel fuel, contributing to emissions from the forestry industry. However, some companies are integrating electric or hybrid propulsion systems into processors and harvesters. This renewable energy helps reduce emissions as well as operating costs. More sustainable power sources aligned with sustainable forestry practices may become a necessity and standard in the future.
Integration of 3D printing technology
3D printing construction using sustainable materials is an emerging trend. Researchers are exploring using this technology to “print” biodegradable tree habitats or seedlingplanters right at the logging site using wood waste as material. Instead of clear-cutting swaths of forests, operators might selectively harvest trees while leaving printed refuges that [fade away as new trees grow.]
While purpose-built forestry equipment like the Lumberjack prioritize operator safety, additional features continue emerging as monitoring technology improves. Cameras, proximity sensors, and even heart monitors built into seats can give equipment operators more awareness and warn them of potential hazards in their work zone. These safety enhancements will only further efforts to achieve zero-incident worksites.