PVC pipes have revolutionized industrial plumbing and fluid transport systems. These versatile plastic conduits offer a winning combination of durability, cost-effectiveness, and adaptability. From chemical processing plants to water treatment facilities, different types of PVC pipe play crucial roles in various industrial applications. Let’s dive into the world of PVC pipes and explore their properties, types, and uses in industrial settings.
Understanding PVC Pipe: Properties, Materials, and Manufacturing
PVC, or polyvinyl chloride, is a synthetic plastic polymer that’s been a game-changer in the piping industry. Its unique properties make it an ideal material for industrial applications. Let’s break down what makes PVC pipes so special.
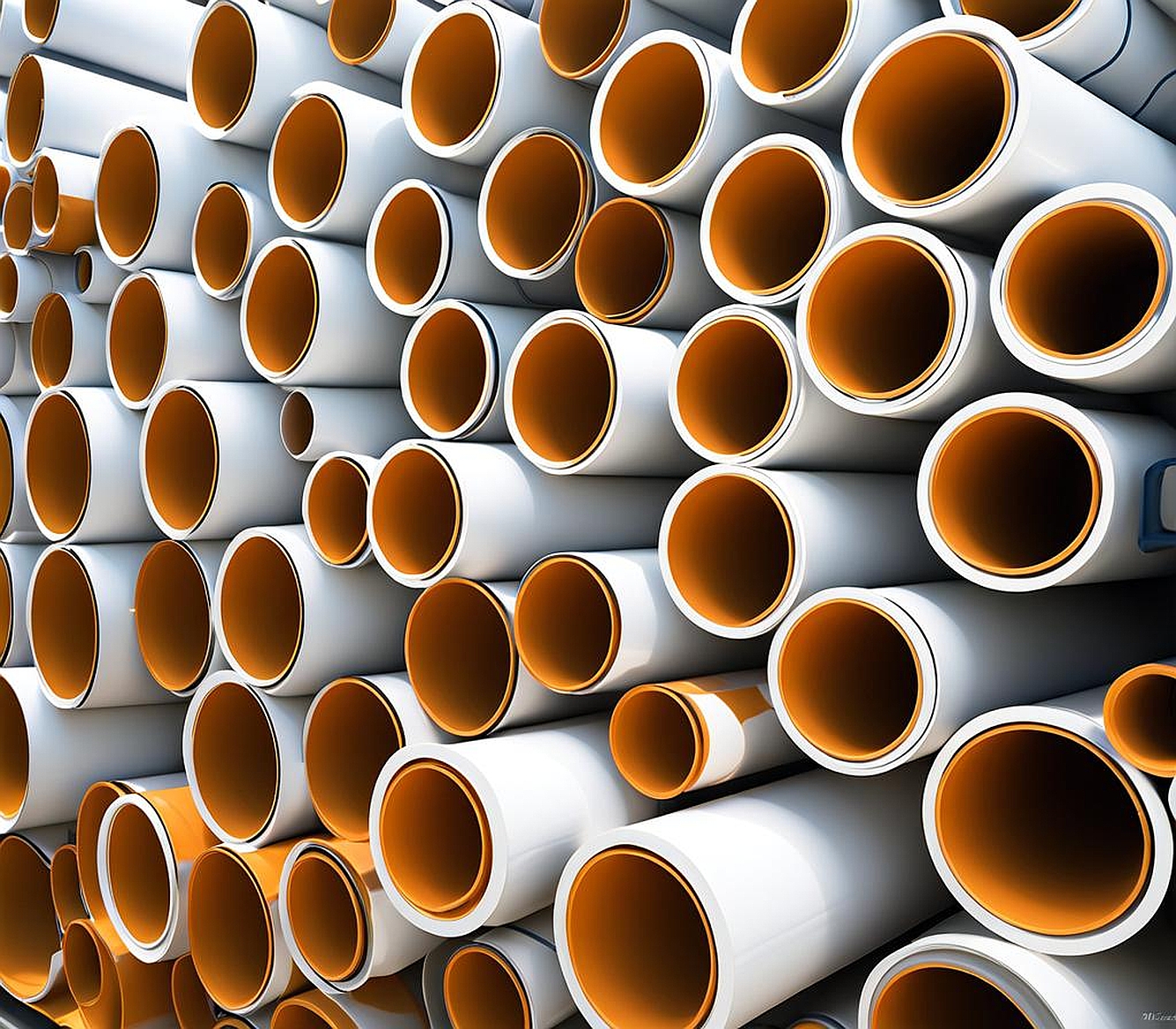
First off, the chemical composition of PVC gives it remarkable strength and durability. The molecular structure of PVC creates a rigid, yet slightly flexible material that can withstand high pressures and resist corrosion. This makes it perfect for transporting a wide range of fluids, including water, chemicals, and even some gases.
One of the standout pvc pipe properties is its resistance to chemical degradation. Unlike metal pipes that can corrode over time, PVC pipes maintain their integrity even when exposed to harsh chemicals. This characteristic is particularly valuable in industrial settings where pipes often come into contact with corrosive substances.
The manufacturing process of PVC pipes is a fascinating blend of chemistry and engineering. It starts with the polymerization of vinyl chloride monomers to create PVC resin. This resin is then mixed with various additives to enhance its properties. Heat stabilizers, for instance, are added to prevent degradation during the extrusion process, while lubricants help in the smooth formation of the pipe.
The mixture is then fed into an extruder, where it’s heated and forced through a die to create the pipe shape. The pipe is then cooled, cut to length, and tested for quality. This process allows for precise control over pvc pipe dimensions and specifications, ensuring consistency and reliability in industrial applications.
One of the key advantages of PVC pipe manufacturing is the ability for pvc pipe customization. Manufacturers can adjust the formulation and extrusion process to create pipes with specific characteristics. This flexibility allows for the production of pipes tailored to particular industrial needs, whether it’s extra chemical resistance for a petrochemical plant or increased pressure ratings for a high-flow water system.
The pvc pipe materials used in industrial applications are typically of higher grade than those used in residential plumbing. Industrial-grade PVC pipes often incorporate additional stabilizers and impact modifiers to enhance their performance under demanding conditions. These pipes are designed to withstand higher temperatures, pressures, and chemical exposures than their residential counterparts.
It’s worth noting that the pvc pipe characteristics can be further modified through post-extrusion treatments. For example, some industrial PVC pipes undergo additional heat treatment to increase their temperature resistance, making them suitable for hot fluid transport in industrial processes.
Property | Advantage in Industrial Use |
---|---|
Chemical Resistance | Withstands corrosive fluids |
Durability | Long service life in harsh conditions |
Customizability | Can be tailored for specific applications |
Cost-effectiveness | Lower installation and maintenance costs |
Understanding these fundamental aspects of PVC pipes sets the stage for exploring the different types and their specific industrial applications. As we delve deeper into the world of industrial PVC piping, we’ll see how these properties translate into practical benefits across various sectors.
Exploring Different Types of PVC Pipe: Grades, Dimensions, and Specifications
When it comes to industrial applications, not all PVC pipes are created equal. The types of pvc pipes used in industrial settings vary widely based on their intended use, the substances they’ll carry, and the environmental conditions they’ll face. Let’s explore the different grades, dimensions, and specifications of PVC pipes commonly used in industry.
First, let’s talk about pvc pipe grades. In the industrial world, you’ll commonly encounter two main grades: Schedule 40 and Schedule 80. These schedules refer to the wall thickness of the pipe relative to its diameter. Schedule 80 PVC pipe has a thicker wall than Schedule 40, making it more suitable for high-pressure applications.
Schedule 40 PVC pipes are the workhorses of many industrial settings. They offer a good balance of strength and cost-effectiveness, making them suitable for a wide range of applications. You’ll find Schedule 40 pipes in water treatment plants, chemical processing facilities, and agricultural irrigation systems.
On the other hand, Schedule 80 PVC pipes are the heavy-duty option. Their thicker walls allow them to withstand higher pressures and provide extra durability. These pipes are often used in industrial processes that involve corrosive chemicals or high-temperature fluids. They’re also commonly used in compressed air systems and high-pressure water lines.
Now, let’s dive into pvc pipe dimensions. Industrial PVC pipes come in a wide range of sizes to accommodate various flow rates and system designs. The most common sizes range from 1/2 inch to 24 inches in nominal diameter. However, you can find PVC pipes as small as 1/8 inch for specialized applications, and as large as 36 inches for major water distribution systems.
It’s important to note that the nominal size of a PVC pipe doesn’t always correspond to its actual dimensions. For example, a 2-inch Schedule 40 PVC pipe has an actual outside diameter of 2.375 inches and an inside diameter of 2.067 inches. Understanding these nuances is crucial when designing industrial piping systems and selecting appropriate pvc pipe fittings.
Speaking of fittings, the world of pvc pipe accessories is vast and varied. From elbows and tees to reducers and flanges, there’s a fitting for every conceivable piping configuration. These fittings are designed to match the schedules and dimensions of the pipes they connect, ensuring a seamless and leak-free system.
When it comes to pvc pipe specifications, there’s more to consider than just size and schedule. Industrial PVC pipes are rated based on their pressure-bearing capacity, typically expressed in pounds per square inch (PSI). For instance, a 2-inch Schedule 40 PVC pipe might have a pressure rating of 280 PSI at 73degF, while the same size in Schedule 80 could handle up to 400 PSI.
Temperature is another crucial factor in PVC pipe specifications. As temperature increases, the pressure rating of PVC pipes decreases. This is why it’s essential to consider both the maximum pressure and temperature of the fluid being transported when selecting PVC pipes for industrial use.
Let’s not forget about the different types of pvc pipe connections. In industrial settings, you’ll encounter several joining methods:
- Solvent welding: This involves using a chemical solvent to fuse PVC pipes and fittings together.
- Threaded connections: Some industrial PVC pipes and fittings come with threads for easy assembly and disassembly.
- Flanged connections: These are used for larger pipes and allow for easy maintenance and replacement of pipe sections.
- Mechanical couplings: These can be used to join PVC pipes to other types of pipes or to create flexible connections in a system.
Understanding these different connection types is crucial for proper pvc pipe installation in industrial settings. Each method has its advantages and is suited to different applications based on factors like pressure requirements, ease of maintenance, and system flexibility.
It’s worth mentioning that there are also specialized types of PVC pipes for specific industrial applications. For example, CPVC (Chlorinated PVC) pipes offer higher temperature resistance than standard PVC, making them suitable for hot water systems in industrial facilities. Another example is PVC-O (Oriented PVC) pipes, which undergo a molecular orientation process to enhance their strength and impact resistance.
The difference in pvc pipe types extends beyond just their physical properties. Some PVC pipes are specifically formulated to meet industry standards for particular applications. For instance, NSF-listed PVC pipes are certified for use in potable water systems, while ASTM-rated pipes meet specific performance criteria for various industrial uses.
As we can see, the world of industrial PVC piping is complex and diverse. From varying grades and dimensions to specialized specifications and connection types, there’s a PVC pipe solution for virtually every industrial piping need. Understanding these differences is key to selecting the right PVC pipe for your specific application, ensuring optimal performance, safety, and longevity in your industrial processes.
Now that we’ve explored the various types and specifications of PVC pipes, let’s dive into their practical applications in industrial settings and the key considerations for installation. The versatility of PVC pipes makes them suitable for a wide range of industrial uses, each with its own unique requirements.
One of the most common pvc pipe applications in industry is water treatment and distribution. In these systems, PVC pipes are used to transport raw water, chemicals for treatment, and the final treated water. The chemical resistance of PVC makes it ideal for handling the various substances involved in water treatment processes. For instance, Schedule 80 PVC pipes are often used for chemical feed lines due to their higher pressure rating and thicker walls, providing an extra layer of safety when dealing with corrosive treatment chemicals.
In the chemical processing industry, PVC pipes play a crucial role in transporting a variety of substances. From acids and bases to solvents and solutions, the chemical resistance of PVC allows it to handle a wide range of materials without degradation. Here, the choice of PVC pipe grade is critical. While Schedule 40 might be sufficient for some low-pressure chemical transfer lines, Schedule 80 is often preferred for its higher pressure rating and added durability.
The food and beverage industry also relies heavily on PVC piping. In these applications, sanitation is paramount. NSF-listed PVC pipes are commonly used for transporting potable water and food-grade materials. The smooth interior surface of PVC pipes resists buildup and makes cleaning easier, helping to maintain the high hygiene standards required in food processing.
When it comes to pvc pipe installation in industrial settings, there are several factors to consider. First and foremost is the compatibility of the pipe with the substance it will carry. This involves not just considering the chemical resistance of the pipe, but also its pressure and temperature ratings. For example, if you’re designing a system to transport hot caustic solutions, you might opt for CPVC pipes for their higher temperature resistance.
The environment in which the pipes will be installed also plays a crucial role in pipe selection and installation. For outdoor installations, UV-resistant PVC pipes should be used to prevent degradation from sunlight exposure. In areas with high ambient temperatures, the pressure ratings of the pipes may need to be de-rated to account for the increased stress on the material.
Proper support is another critical aspect of PVC pipe installation in industrial settings. Unlike metal pipes, PVC pipes can sag over time if not adequately supported. The spacing of pipe hangers and supports should be calculated based on the pipe size, schedule, and the weight of the fluid being transported. This ensures the long-term integrity of the piping system and prevents stress-related failures.
When it comes to joining PVC pipes in industrial applications, the choice of connection method can significantly impact the system’s performance and longevity. Solvent welding is the most common method for smaller pipes, creating a strong, leak-proof joint. However, for larger pipes or in situations where disassembly might be necessary, flanged or mechanical connections are often preferred.
It’s worth noting that pvc pipe usage in industrial settings often requires specialized installation techniques. For instance, expansion joints may need to be incorporated into long runs of pipe to accommodate thermal expansion and contraction. Similarly, proper venting and drainage points should be included in the system design to prevent air locks and allow for system maintenance.
The pvc pipe characteristics that make it ideal for one application might make it less suitable for another. For example, while PVC’s flexibility can be an advantage in some situations, allowing for easier installation in tight spaces, it can be a drawback in high-temperature applications where the pipe might soften and deform. This is why understanding the specific requirements of your application is crucial in selecting the right type of PVC pipe.
When it comes to pvc pipe sizes, industrial applications often require larger diameters than those commonly used in residential plumbing. Pipes with diameters of 8 inches, 12 inches, or even larger are not uncommon in industrial settings. These larger pipes require specialized handling and installation techniques, often necessitating the use of heavy machinery for placement and joining.
In conclusion, the world of industrial PVC piping is vast and complex. From the various types of PVC pipes available to the myriad of applications they serve, there’s a lot to consider when designing and installing a PVC piping system for industrial use. By understanding the properties, specifications, and installation requirements of different PVC pipes, industrial engineers and designers can create efficient, durable, and cost-effective piping solutions for a wide range of applications. Whether you’re dealing with aggressive chemicals, high-pressure fluids, or sensitive food products, there’s likely a PVC pipe solution that fits your needs. The key lies in carefully analyzing your specific requirements and choosing the right pipe for the job.