Joining ABS (Acrylonitrile Butadiene Styrene) to PVC (Polyvinyl Chloride) presents unique challenges in the world of plastic bonding. While these materials are both widely used in plumbing and construction, their distinct chemical compositions make gluing abs to pvc a topic of debate among professionals. I’ve spent years working with various plastics, and I can tell you that achieving a strong abs pvc joint isn’t as straightforward as it might seem. Let’s dive into the nitty-gritty of this process, exploring the ins and outs of abs to pvc bonding, and uncover the best practices for creating a durable connection between these two materials.
Understanding ABS and PVC Materials: Properties and Differences
Before we jump into the specifics of gluing ABS to PVC, it’s crucial to understand the nature of these materials. ABS and PVC are like distant cousins in the plastic family – related, but with distinct personalities that don’t always mesh well.
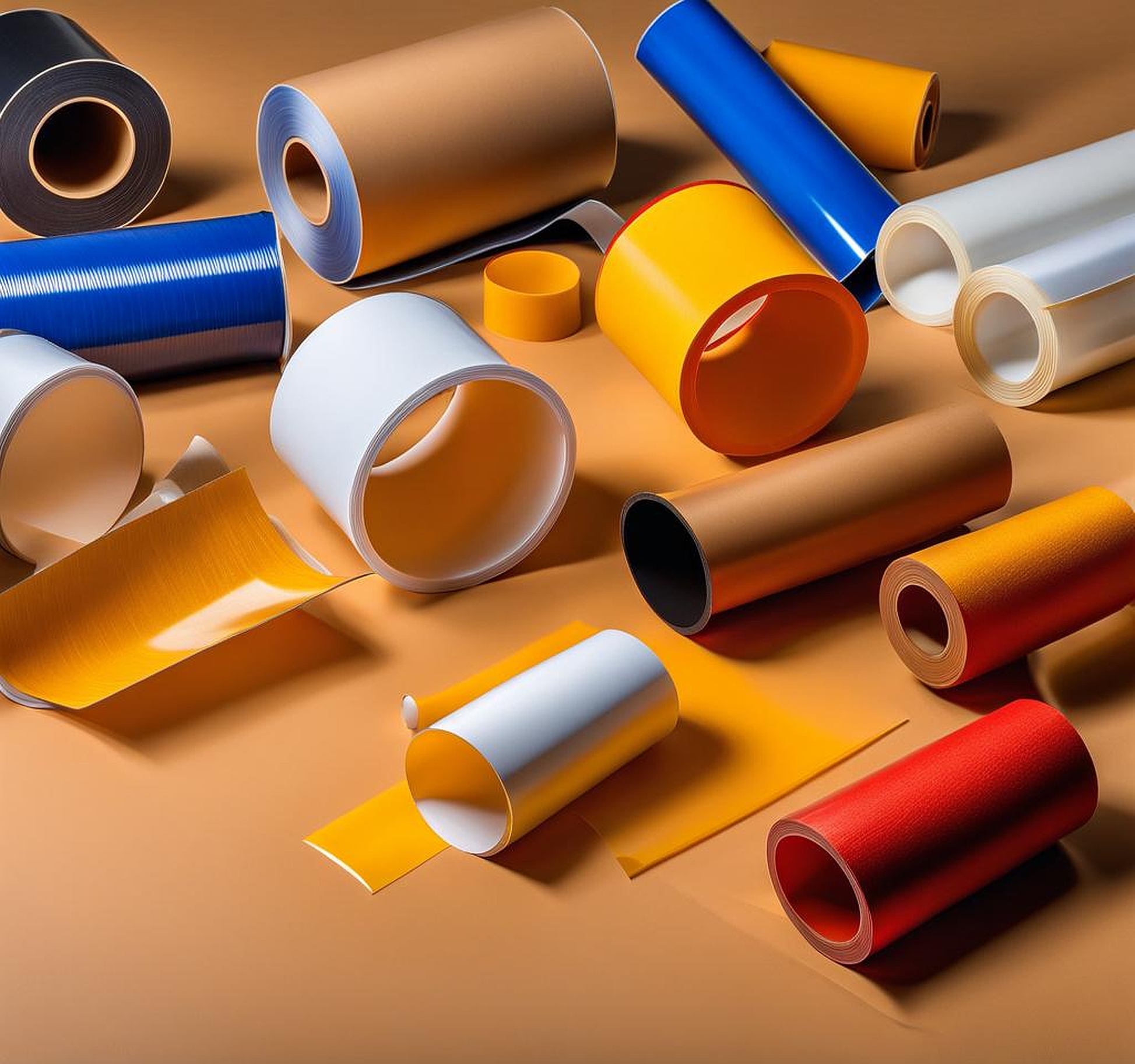
ABS, or Acrylonitrile Butadiene Styrene, is a tough cookie. It’s known for its impact resistance and durability. I remember working on a project where we needed a material that could withstand frequent bumps and knocks, and ABS was our go-to choice. It’s often used in automotive parts, electronics enclosures, and even those beloved LEGO bricks. The abs plastic bonding process typically involves using specialized abs glue, which essentially melts the surfaces together.
On the other hand, PVC, or Polyvinyl Chloride, is the chameleon of the plastic world. It’s versatile, cost-effective, and can be found in everything from plumbing pipes to credit cards. PVC comes in two flavors: rigid and flexible. The rigid type is what we’re dealing with when we talk about pvc pipe abs attachment. PVC is less impact-resistant than ABS but offers excellent chemical resistance and is easier to work with in many applications.
The key difference that affects abs to pvc bonding lies in their chemical structure. ABS is a thermoplastic terpolymer, while PVC is a thermoplastic polymer. This distinction means that the solvents that work well for bonding ABS might not be as effective on PVC, and vice versa. It’s like trying to use the same key for two different locks – it just won’t work efficiently.
Moreover, the abs glue strength differs significantly from PVC adhesives. ABS cement is formulated to create a strong molecular bond by partially dissolving the ABS surface. PVC cement works similarly but is tailored for PVC’s unique composition. When we try to use these adhesives interchangeably or attempt to create an abs pvc composite, we’re essentially asking for trouble.
Challenges of Joining ABS to PVC: Compatibility and Strength Considerations
Now, let’s talk about the elephant in the room – the challenges of creating a strong abs bond with PVC. It’s not impossible, but it’s certainly not a walk in the park either. The main issue stems from the chemical incompatibility between these two materials.
When I first attempted pvc abs welding, I quickly realized that traditional methods weren’t going to cut it. The problem lies in the different solvents used for each material. ABS requires a stronger, more aggressive solvent than PVC. Using ABS cement on PVC can lead to a weakened joint, while PVC cement might not effectively bond to ABS at all.
Another challenge is the difference in expansion and contraction rates between ABS and PVC. Temperature fluctuations can cause these materials to move at different rates, potentially stressing and weakening the joint over time. I once worked on a project where we ignored this factor, and let’s just say the results weren’t pretty – we ended up with leaks and failures that could have been avoided.
The strength of an abs pvc joint is also a significant concern. In plumbing applications, for instance, these joints need to withstand pressure, temperature changes, and sometimes even physical stress. A weak bond can lead to leaks, structural failures, or even complete separation of the materials.
Moreover, building codes and regulations often frown upon joining these dissimilar materials. In many jurisdictions, it’s not considered an approved practice for plumbing systems. This legal aspect adds another layer of complexity to the challenge of gluing abs to pvc.
Despite these challenges, there are situations where joining ABS to PVC is necessary. In retrofit projects or repairs where replacing an entire system isn’t feasible, creating a reliable abs to pvc attachment becomes crucial. This is where understanding the right techniques and products becomes invaluable.
Selecting the Right Adhesive: ABS-PVC Cements and Specialized Bonding Agents
Choosing the right adhesive is like picking the perfect dance partner – get it right, and everything flows smoothly; get it wrong, and you’re stepping on toes. When it comes to abs glue to pvc applications, we’re looking for a special kind of chemistry.
First off, let’s talk about the star of the show: transition cement. This is a specialized pvc abs adhesive designed specifically for joining these dissimilar materials. It’s like a linguistic interpreter, able to communicate effectively with both ABS and PVC. I’ve used transition cements in several projects, and while they’re not a magic bullet, they do provide a more reliable bond than using standard ABS or PVC cement alone.
These transition cements typically contain a blend of solvents that can partially dissolve both ABS and PVC surfaces. This creates a sort of “fusion zone” where the two materials can intermingle at a molecular level. The result? A stronger abs pvc joint than you’d get with mismatched adhesives.
However, it’s crucial to note that not all transition cements are created equal. Look for products specifically labeled for ABS to PVC bonding. Some brands even offer different formulations for wet and dry applications, which can be a game-changer in certain situations.
Another option that’s gained traction in recent years is the use of epoxy-based adhesives. These two-part systems can create a strong mechanical bond between ABS and PVC. While they don’t work by dissolving the plastics like solvent cements do, they can provide impressive abs glue strength in certain applications.
It’s worth mentioning that PVA (Polyvinyl Acetate) adhesives, often suggested for various plastic bonding tasks, are generally not suitable for abs to pvc bonding in plumbing or high-stress applications. While PVA for ABS might work for craft projects, it lacks the chemical resistance and strength needed for more demanding uses.
When selecting an adhesive, always consider the specific requirements of your project. Factors like temperature range, pressure resistance, and chemical exposure can all influence which product will perform best. And remember, while a good adhesive is crucial, it’s only part of the equation. Proper surface preparation and application techniques are equally important for achieving a reliable abs pvc sealing.
Preparation Techniques for Optimal ABS to PVC Attachment
Alright, now we’re getting to the nitty-gritty of abs to pvc attachment. Proper preparation is like laying a good foundation – skip it, and your whole project might come tumbling down. I’ve seen too many DIY enthusiasts and even some pros rush this step, only to end up with weak joints and frustrated faces.
First things first: cleanliness is next to godliness when it comes to plastic bonding. Both the ABS and PVC surfaces need to be spotless. I’m talking squeaky clean, folks. Any dirt, grease, or even moisture can interfere with the bonding process. I always start by wiping down the surfaces with a clean, dry cloth. For stubborn grime, a quick wipe with acetone or another appropriate solvent can work wonders. Just be sure to let it evaporate completely before moving on.
Next up is surface preparation. This is where many people go wrong when attempting pvc pipe abs attachment. Both ABS and PVC benefit from a bit of roughing up. Use fine-grit sandpaper to lightly scuff the bonding areas. This increases the surface area and gives the adhesive more “teeth” to grip onto. Just don’t go overboard – we’re aiming for a light scuff, not a deep scratch.
Now, here’s a pro tip that’s served me well: use a primer before applying the adhesive. A good primer can significantly enhance the abs plastic bonding process. It helps to soften the surface of the plastic, allowing for better penetration of the adhesive. For ABS to PVC connections, look for a universal or transition primer that’s compatible with both materials.
Timing is crucial in this process. Once you’ve applied the primer, you’ve got a limited window to apply the adhesive and join the pieces. I like to work in small sections to ensure I’m not racing against the clock. It’s better to take your time and get it right than to rush and end up with a weak joint.
Temperature and humidity can also play a role in the preparation process. Extreme temperatures can affect the curing time of adhesives, while high humidity can introduce moisture that interferes with bonding. Aim to work in a controlled environment when possible, or at least be aware of how the conditions might impact your project.
Lastly, don’t forget about proper alignment. Before you apply any adhesive, do a dry fit to ensure everything lines up correctly. There’s nothing more frustrating than realizing your pieces don’t quite match up after you’ve already applied the glue. A little planning goes a long way in achieving a professional-looking and structurally sound abs pvc joint.
Now that we’ve covered the groundwork, let’s dive into the actual process of gluing ABS to PVC. I’m going to walk you through this step-by-step, sharing some hard-earned wisdom along the way. Remember, practice makes perfect, so don’t be discouraged if your first attempt isn’t flawless.
Step 1: Measure and Cut Before we even think about gluing, make sure your pieces are cut to the correct size. For pipes, use a pipe cutter for clean, square cuts. If you’re working with sheets, a fine-toothed saw or a utility knife (for thinner sheets) will do the trick. Always measure twice and cut once – it’s an old adage, but it’s saved my bacon more times than I can count.
Step 2: Clean and Prepare As we discussed earlier, cleanliness is crucial. Wipe down all surfaces with a clean, dry cloth. For extra assurance, use a solvent cleaner compatible with both ABS and PVC. Once clean, lightly sand the bonding areas with fine-grit sandpaper. This step is vital for achieving a strong abs bond.
Step 3: Apply Primer Using a suitable applicator (usually provided with the primer), apply a thin, even coat of transition primer to both the ABS and PVC surfaces. Work quickly but carefully – the primer starts working immediately.
Step 4: Apply Adhesive Within a minute of applying the primer, it’s time for the pvc abs cement. Using the applicator provided (usually a dauber or brush), apply a generous coat of adhesive to both surfaces. Make sure to cover the entire bonding area evenly.
Step 5: Join the Pieces Immediately after applying the adhesive, join the ABS and PVC pieces together. If you’re working with pipes, give them a quarter turn as you push them together to ensure even coverage. Hold the pieces firmly in place for at least 30 seconds.
Step 6: Allow to Cure This is where patience comes into play. While the initial bond forms quickly, full curing can take 24 hours or more. Avoid putting any stress on the joint during this time.
Pro Tips: – Work in a well-ventilated area. The fumes from primers and cements can be potent. – For larger projects, use alignment tools to ensure everything stays in place while curing. – In colder temperatures, you might need to extend curing times. – For added security in high-stress applications, consider using mechanical fasteners in addition to the adhesive bond.
Remember, while these techniques can create a functional abs pvc composite, it’s not a substitute for proper plumbing practices in code-regulated applications. Always consult local building codes and, when in doubt, seek professional advice.
By following these steps and keeping the unique properties of ABS and PVC in mind, you’ll be well on your way to creating strong, reliable bonds between these two materials. Whether you’re tackling a DIY project or working on a professional installation, these best practices for gluing abs to pvc will serve you well.