We’ve all experienced that frustration of coming home to a sweltering house, only to find that the thermostat clearly shows the temperature is set to off. Yet somehow the heating system didn’t get the message and continues pumping out heat. Dealing with a heating system that won’t quit despite flipping the off switch can be maddening. But before you give in to thermostat rage, understanding what causes this phantom heating effect can help resolve issues faster.
From faulty thermostats to electrical shorts triggering heating calls, we’ll explore the range of culprits that could be behind a heating system that defies its thermostat master. With some key troubleshooting steps and home maintenance best practices, you can wrangle runaway home heat and restore peaceful temperature control.
Faulty Thermostats
The thermostat acts as the main interface between users and heating/cooling systems. Using built-in sensors, programming, and display controls, it should switch connected equipment on or off based on home conditions and settings. When the thermostat itself malfunctions, it can fail to properly regulate equipment.
How Do Thermostats Work?
Thermostats contain special switches, sensors, wiring, and software to communicate equipment operating statuses. Here’s a quick rundown of key components:
- Temperature Sensor: Detects indoor ambient temperatures
- Heat/Cool Switch: Selects heating or A/C modes
- Wires: Carries electric signals to heating/cooling equipment
- Programming: Contains automated temps/schedules
Based on how the sensor interacts with user settings and programs, electrical signals are (or aren’t) sent to climate equipment via wiring. For example, once the target room temperature is reached, the sensor triggers the thermostat to stop the “call for heat/cool” signal. Pretty straightforward when all parts work properly!
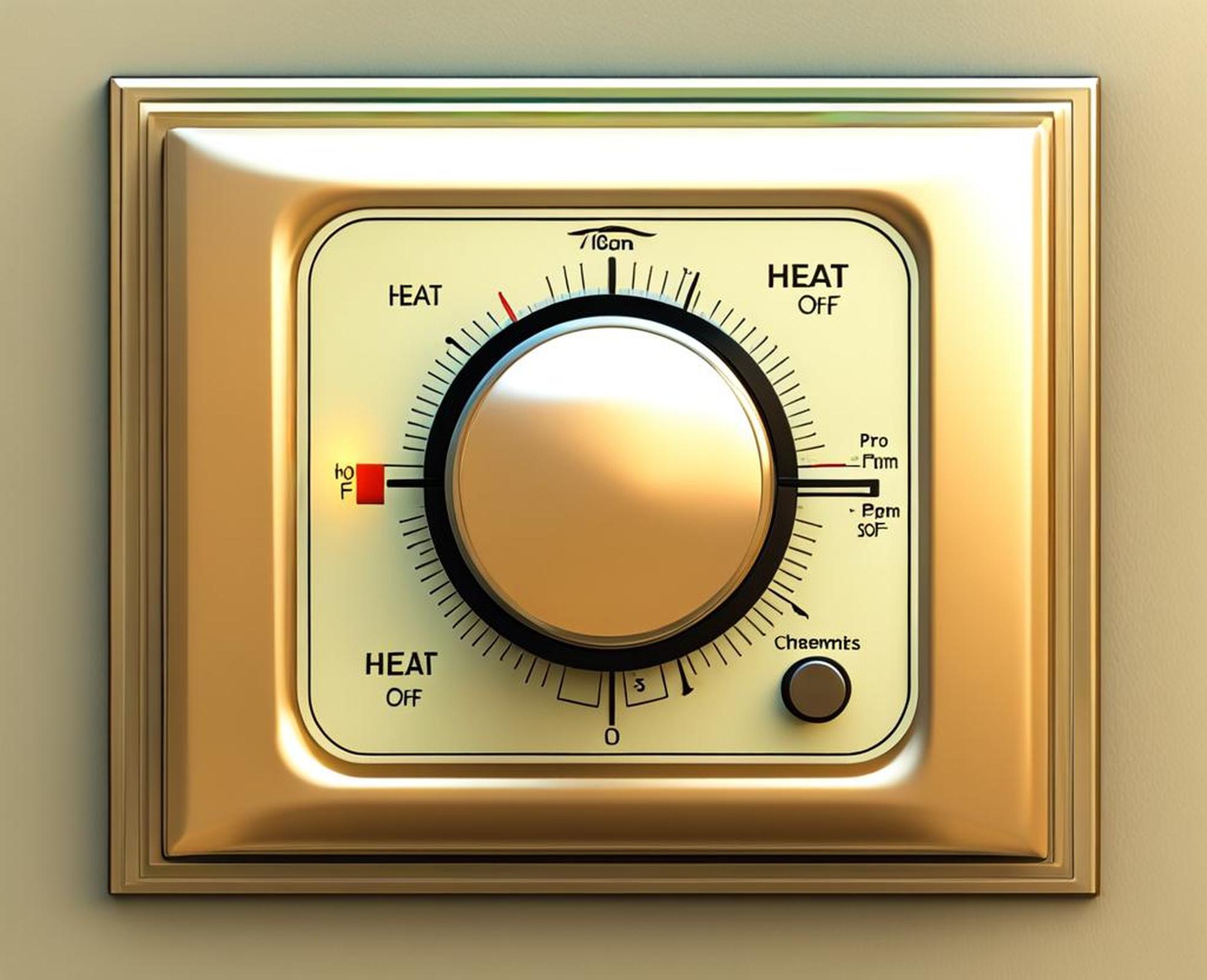
Common Thermostat Issues
Like any piece of technology, thermostats can experience glitches or failures with regular wear and tear over 5-10 years. Here are some typical problems that cause unreliable temperature control:
- Damaged Wiring: Frayed or broken wires won’t properly carry electric signals.
- Corroded/Broken Sensors: Faulty temperature or mode sensors give inaccurate readings.
- Software Errors: Bugs or crashes in program settings lead to operational failures.
- Power Surges: Electrical spikes fry delicate thermostat components.
Issues like these prevent the thermostat from reliably monitoring home environments and controlling connected equipment. So even when powered “off,” misfires from damaged components can still activate heating or cooling.
Testing Your Thermostat
Before replacing your thermostat, some simple checks can confirm if it’s truly malfunctioning or needs reprogramming:
- Adjust temperature setting well below room reading – should turn unit off
- Change system mode from Heat to Off – heating should stop
- Check wire connections are tight on control board
- Replace old batteries if applicable
- Factory reset thermostat to clear any software glitches
If adjusting settings and inputs fails to properly turn the connected system on or off, the thermostat itself likely has deeper issues.
Replacing Faulty Thermostats
For damaged or outdated thermostats, replacement is the most cost-effective solution for restore reliable function. Handling the swap yourself averages $100-$250 for equipment + 1-3 hours of effort. Hiring an HVAC pro boosts the price to $200-$500 depending on home complexity. As long as compatible wiring exists, installing a new programmable or smart WiFi-enabled upgrade is straightforward.
Heating System Controls
While a clear thermostat mishap often causes phantom heating, the root problem can also lie with heating equipment controls instead. Boilers, furnaces, and heat pumps have dedicated control boards that could malfunction and override normal off signals.
How Heating Controls Operate
Advanced heating systems include these key components to manage operation:
- Control Board: Central computer that oversees heating sequences
- Relays: Switch gears on/off based on control signals
- Sensors: Detect performance stats to report back
Ideally the thermostat feeds usage guidelines to the central control board, which then flips heating relays on or off accordingly. If relays or sensors fail, the board can misinterpret statuses and activate heat incorrectly. Or if its programming gets corrupted, it may disregard normal off signals.
Testing Controls and Sensors
To check if a heating system’s control board or related components are malfunctioning:
- Turn thermostat mode to Off
- Check if heating relays remain activated
- See if sensors report abnormal performance data
- Review control panel for error codes
Any equipment staying on despite an Off status indicates a board, relay, or sensor problem overriding normal operation. The system requires repair or replacement of damaged controls before it can resume properly responding to thermostat inputs.
Diagnosing Heat Circulation Issues
Interference with a heating system’s internal circulation components can also lead to unexpected heat discharges. Whether air vents remain open or water valves stick, problems in these areas allow heating effects to continue traveling through a system uncontrolled.
How Heat Circulation Works
For both hot water radiators and forced air furnaces, valves/vents open or close to circulate warmth on demand:
- Radiators: Zone valves regulate hot water flow to different radiators.
- Forced Air: Registers or dampers channel air through vents.
Ideally when heating calls stop, these circulation pathways close off to contain heat energy only where still needed. If components controlling heat transfer remain stuck open, warmth will continue permeating through the system despite equipment powering down.
Checking for Stuck Circulation Components
To test if radiator valves or air dampers are failing to close properly when heat calls cease, check if radiators/vents remain hot to touch a few hours after switching the thermostat or system off. Continued heat emanating from these areas likely indicates a stuck open component manually needs closing.
Fixing Common Circulation Problems
Repair strategies depends on the specific type of heating system:
- Radiators: Adjust zone valves manually, drain and flush radiators, replace broken valve parts.
- Forced Air Systems: Double-check vent dampers are shutting fully, inspect ducts for obstructions, replace damaged vents/registers.
Getting both routine seasonal maintenance and investigating odd activity can catch circulation problems before they progress.
Electrical Shorts and Phantom Calls for Heat
Errant voltage in system wiring can mimic normal signals that trigger heating equipment activity regardless of actual home conditions or demands. These “phantom calls for heat” offer no thermostat override abilities until the short gets addressed.
What Causes Phantom Heating Activation?
Random voltage spikes in heating system wires can happen from:
- Exposed copper wiring contacting metal surfaces
- Damaged wire insulation allowing current leakage
- Overloads from frequent equipment cycling
- Flaws in electrical workmanship
When loose voltage happens to form a complete circuit in the specific configuration that heating systems recognize as a call for operation, it essentially creates false activation demand. Just a quirk of crossed wires!
Checking for Short Circuits
To test if errant voltage is triggering heating system activity:
- Turn off power to equipment at breaker
- Disconnect thermostat wiring from control board
- Restore system power
If heating operation persists despite being disconnected from the thermostat’s control influence, it points to a short circuit somewhere in the system wiring erroneously calling for heat during power cycles.
The Dangers of Electrical Shorts
While phantom heating activations from shorts seem harmless, allowing them to continue stresses equipment and can cause compounding issues over time, namely:
- Higher utility bills from phantom load draws
- Premature wear on heating elements and fans
- Melting wire insulation and risk of fires
As soon as errant voltage appears as a possible root cause, prompt troubleshooting by an HVAC professional helps correct shorts before extensive damages or safety hazards develop.
Getting Help from HVAC Technicians
For thermostat, heating control, or electrical issues that DIY measures fail to resolve, leverage HVAC pros to tackle tricky diagnostic and repair needs.
What Happens During Service Calls?
When technicians visit to inspect heating systems with minds of their own, you can expect a standard process:
- Discussion of equipment history and problem specifics
- Visual checks of thermostat, wiring, and controls
- Power cycle tests observing system responses
- Adjustment of components not properly calibrated
- Recommendations for repair or replacement as needed
With their advanced technical skills and tools, HVAC companies can hone in on issues more accurately to restore normal equipment function.
Prepping for Technician Visits
Making the most of service calls to troubleshoot heating systems requires some savvy prep work:
- Note what specific settings/scenarios do and don’t trigger problems
- Document all heating equipment models plus past issues
- Research and collect any manuals available
- Test thermostat ahead and gather pictures of readings/settings
Equipping technicians with detailed background information better guides their workflow focus and parts needs ultimately saving service time and costs.
Understand Repair Costs
While solving phantom heating issues requires tailored solutions, typical HVAC service rates average:
- Service Call Fee: $50 – $100
- Hourly Rate: $70 – $200
- Thermostat Swap: $200 – $500
- Control Board Fix: $400+
- Equipment Replacement: $2,000+
Discuss budget thresholds when establishing project scope. Technicians can guide prioritization if comprehensive repairs exceed affordability.
Ask These Key Questions
To pick the right solutions from a technician’s recommendations, get clear on:
- Is the issue intermittent or consistent?
- What components require repair or replacement?
- What risks come with partial fixes?
- How will new equipment integrate with existing setups?
- What permits or additional labor applies?
- What other home upgrades deserve consideration?
Addressing these details from the start prevents mid-project surprises and ensures heating systems meet unique home needs.
Preventing Future Thermostat Issues
Beyond tackling immediate heating system problems, smart maintenance and home upgrades provide protection against repeat phantom heating episodes.
Fall System Checks
Make these routine furnace/boiler preparations before cold weather hits:
- Replace air filters
- Test heating at multiple thermostat settings
- Compare control panel data year-over-year
- Clear debris/obstructions around vents
- Check wire and pipe leak points
- Inspect flame quality
Early season heating trials identify problems needing repair before systems run extensive hours keeping homes comfortable through winter.
Electrical Protection Upgrades
Hardening electrical systems against power fluctuations reduces odds of shorts disrupting heating performance down the road:
- Surge Protectors: Capture power spikes from reaching controls.
- Dedicated Heating Circuits: Prevents overloads tripping wires.
Improving stability of energy supplied to heating equipment minimizes administrator disruption over years of use.
Smart Home Heating Controls
Network-enabled WiFi thermostats add monitoring and customization abilities that minimize missed heating failures:
- Real-time performance alerts to homeowners
- Ability to change settings remotely
- Advanced humidity/occupancy-aware programs
The latest smart home technologies give users more transparent insight and control over heating system behaviors before unchecked issues escalate.
Dealing with heating systems that seem to blast away despite clear off signals strains both home comfort and sanity. But whether the culprit is a faulty thermostat, failing circulatory components, or electrical shorts, identifying the true root cause gets resolution one step closer.