Acrylonitrile butadiene styrene (ABS) plastic is commonly used for 3D printing, prototypes, and fabrication projects where durability and heat resistance are needed. However, successfully cutting ABS sheets and parts over 1/2″ thick presents challenges compared to thinner plastics.
Incorrect techniques can cause costly cracking, chipping, or shattering. By understanding the unique properties of ABS plastic and following professional methods, you can achieve clean precise cuts in thick ABS every time.
Assess the Plastic Prior to Cutting
Before choosing cutting tools or making any cuts:
- Carefully measure ABS plastic thickness using calipers and determine appropriate cutting methods
- Inspect for internal stresses which may lead to cracking when pressure is applied
- Consider final use to allow for blade kerfs and tight tolerance needs
These simple first steps save time, cost, and frustration down the road.
Secure Properly with Clamps
All professional ABS plastic cutters emphasize proper sheet securing to prevent vibration, slipping, or binding during cuts:
- Clamps : Bar clamps, spring clamps, C-clamps, or vises hold flat sheets firmly to a level workbench.
- Adhesives : Double-sided tapes or vacu-seal adhesives can secure irregular ABS shapes.
- Guide Holes : Drilling starter holes relieves internal tension so cutting tools don’t cause stress cracks.
ABS Thickness | Recommended Securing Method |
---|---|
Less than 1/2″ | Light clamping or vise with guide holes |
1/2″ to 1″ | Secure clamps with adhesive tapes plus holes |
Over 1″ thick | Heavy clamping in vises with guide holes |
Adequate securing takes a few extra minutes but prevents cut failures or accidents down the road.
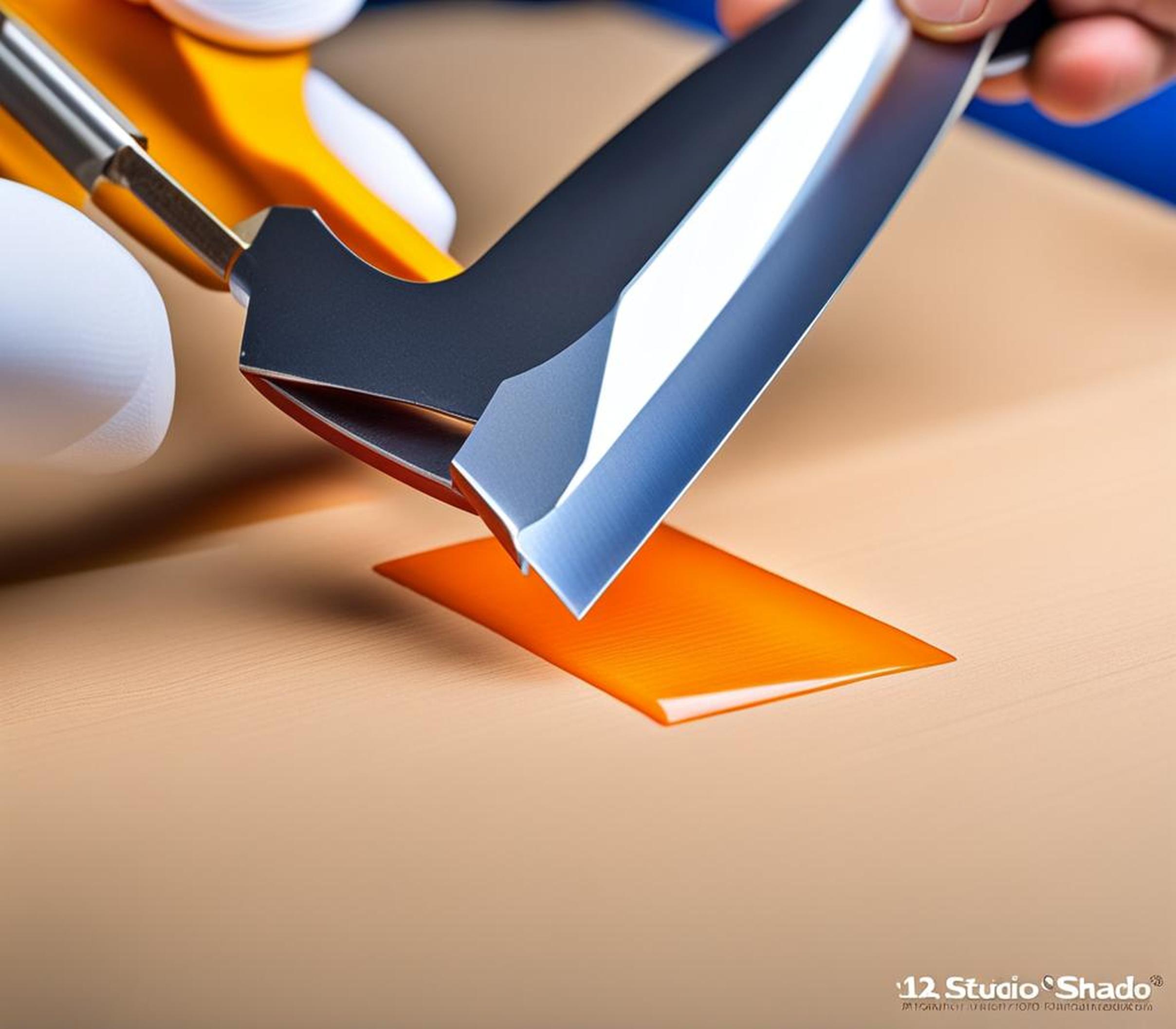
Cutting Method Options for Thick ABS
Hot Knives
Hot knife cutters use an electrically heated blade to melt rather than saw through thermoplastics like ABS sheets less than 1/4″ thick. Benefits include:
- Straight smooth cuts without jagged edges
- Easily cuts detailed shapes and curved contours
- No plastic dust or shards created
Use low temperature settings (200degC or 392degF) and steady slow passes to achieve clean professional cuts.
Circular Saws
Standard circular saws cut thicker plastics with either an abrasive or toothed blade. Key tips when circular saw cutting include:
- Using fine 80+ tooth carbide blades prevents rough edges prone to cracking
- Multi-pass cuts – partially cutting through ABS in several light passes avoids chip-out.
- Employing dust collection and wearing PPE for carcinogenic ABS dust.
Jigsaws
For navigating curves or wherein circular saws risk blade deflection, jigsaws are the top choice. Seek jigsaws with:
- Slow blade speeds under 800 SPM to prevent melting
- Fine-toothed blades (25+ TPI) made for plastics
- Variable orbits for angled cutting control
Quality jigsaw cutting means no dragging or bending – let blades do clean cutting.
Bandsaws
Vertical bandsaws with long cutting widths excel cutting thick flat ABS sheets thanks to:
- Narrow blade kerfs as small as 1/16″
- Slow feed rates under 5 IPM to prevent cracking
- High tension for straight cuts
Downsides of bandsaws include inability to do detail or curve cuts.
Cutting Technique Guidelines by ABS Thickness
Under 1/2″ ABS Sheets
For thin ABS plastic sheets:
- Use sharp hobby knife, razor blade, or fine-toothed saw
- Cut on level rigid cutting mat for control
- Secure with spring clamps and drill starter holes inside any tight curves
1/2 to 1 Inch ABS Plastic
In the 1/2″ to 1″ thickness range:
- Quality jigsaw on slowest setting with 24+ TPI blade
- Cut slowly to prevent edge chipping or melting
- Clamp pieces and consider an adhesive backer for support
Over 1 Inch Thick ABS Slabs
For ABS plastic exceeding 1″ in thickness:
- Use circular saws with guides for long straight cuts
- Reduce standard saw blade exposure to 1/4″ for a narrow kerf cut
- Make several light passes until cut fully penetrates through
Attempting one-pass cuts in thick ABS plastic often causes stress cracks or roughness. Patience pays off.
Preventing Cracks When Cutting
To prevent frustrating cracks, chips, or uneven edges:
- Sharp tools – Dull blades require more cutting force and bind in thick plastics
- Smart layouts – Allow for blade kerf widths so pieces meet cleanly
- Tension relief – Drill small holes just inside cut lines easing internal stress
Rushing any cutting job spells trouble. Go slowly and focus on precision.
Finishing the Cut Edges
For smooth sanded edges and professional watertight bonds try:
- Light filing or 150+ sandpaper to ease saw marks
- Solvent gluing compatible ABS pieces together
- Deburring tools for removing sharp cut edge ridges
Proper ABS edge finishing takes things to the next level.
Pro Tips from Plastic Cutting Experts
We asked professional plastic fabricators for their top ABS cutting recommendations:
Rhys Kemp, CNC Shop Foreman
“Getting clean curves in 1/2 inch ABS means clamping it down twice as hard as you think necessary. Then drill tiny starter holes right on the cut line corners. Finally, use a 14 TPI jigsaw blade lubed with WD-40 for smooth low-friction cutting.”
Devon Mack, Plastics Engineer
“My secret weapon cutting 3/4 inch ABS sheets is using a plywood backer board held flush to prevent bottom edge chip-out. Self-fusing silicone tape secures irregular shaped ABS pieces to the plywood for jigsaw cutting intricate shapes crack-free.”
Frequently Asked Questions
What are signs my ABS plastic is highly stressed and prone to cracking during cuts? Stressed ABS plastic may have slightly warped shape or show white stress lines across surfaces. Tapping gently reveals a “tinny” vibration sound versus solid thud of stable ABS. Stressed plastics require extra precaution in cutting and drilling to prevent failures. Can I cut ABS sheets on a tablesaw or chopsaw instead? It’s not advisable for thick ABS plastic. The force of aggressive teeth can cause both rough tear-outs or cracks in the ABS. Band, jig or circular saws all provide more control when cutting thick plastics. Is there an optimal blade TPI (teeth per inch) for cutting ABS sheets? As a general rule, aim for 80+ teeth carbide blades when using circular saws on ABS plastic. For jigsaws in ABS plastic, 25-35 fine teeth per inch blades yield the best results. Just ensure blades specifically designed for cutting plastics.
When in doubt about the optimal blade or feed rates, do small tests in scrap materials first. Check cut edge quality before tackling final ABS project pieces.
Cutting through thick ABS plastic presents unique challenges other materials don’t. Minding special properties like high internal tension means avoiding cut-related cracking or expensive scrapped projects.
By assessing parts carefully beforehand, securing sheets properly, and using recommended techniques matched to exact ABS plastic thickness, pristine cuts happen reliably.
Patience and the right specialty tools turn frustration into fabrication success when cutting ABS plastic. Follow these professional methods for satisfying smooth, burr-free cuts on your next thick ABS project.